Laser soldering method
“Laser soldering method & theory”
An advancing and developing next-generation soldering method
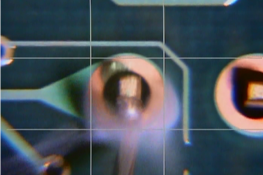
– Laser soldering, the newest soldering method, now gaining the world’s attention –
Laser soldering is garnering attention as a new method. However, the heat application principle and other aspects differ from contact soldering. Therefore, tip soldering cannot be simply replaced to laser soldering. Caution is needed, because a laser’s benefits might be lost unless it is properly used with knowledge of laser soldering’s theory and characteristics. This section explains the basic theory of laser soldering method and the points about which care must be taken.
– What is the difference between a “surface heat generation” and ” thermal conduction”? –
In soldering, tip soldering is basically a 3 step process that encompasses pre-heating of soldering points, applying heat to supply the solder, and then post-heating to shape the solder and finish it. This workflow is the same whether using iron tip soldering or laser soldering, but the method of applying heat to supply the solder differs, and this is very important to understand.
[Tip soldering process]
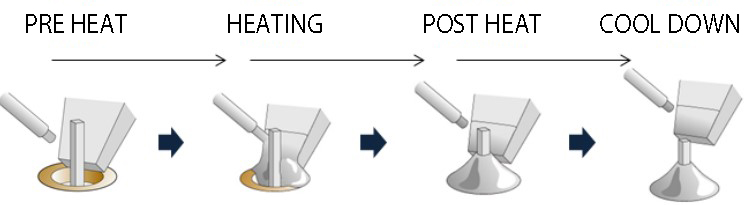
[Laser soldering process]
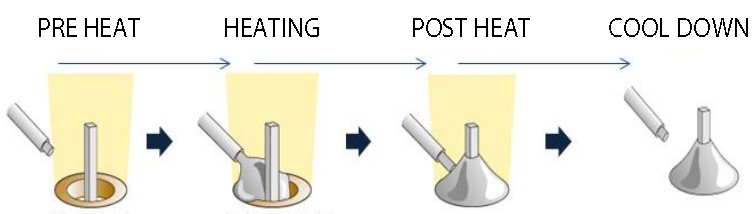
Two different heat application principles
Tip soldering process
- The tip is heated to around 350C / 662F.
- The tip is placed onto the soldering point and heat is applied up to the melting temperature (heat transfer)
- Solder is supplied.
Laser soldering process
- The laser illuminates the soldering point.
- The illuminated area emits heat (surface heat emission).
- The heat transfers into the surrounding area and is raised to the melting temperature.
- Solder is supplied
Contact soldering, heat is transferred from the iron tip, and in laser soldering, the lighted area generates heat. In contact soldering, the tip’s own temperature is the upper limit, but in laser soldering, if laser shot is continuously pointed at one place, the temperature will unlimitedly rise.
Therefore, the light energy and time interval must be managed with care.
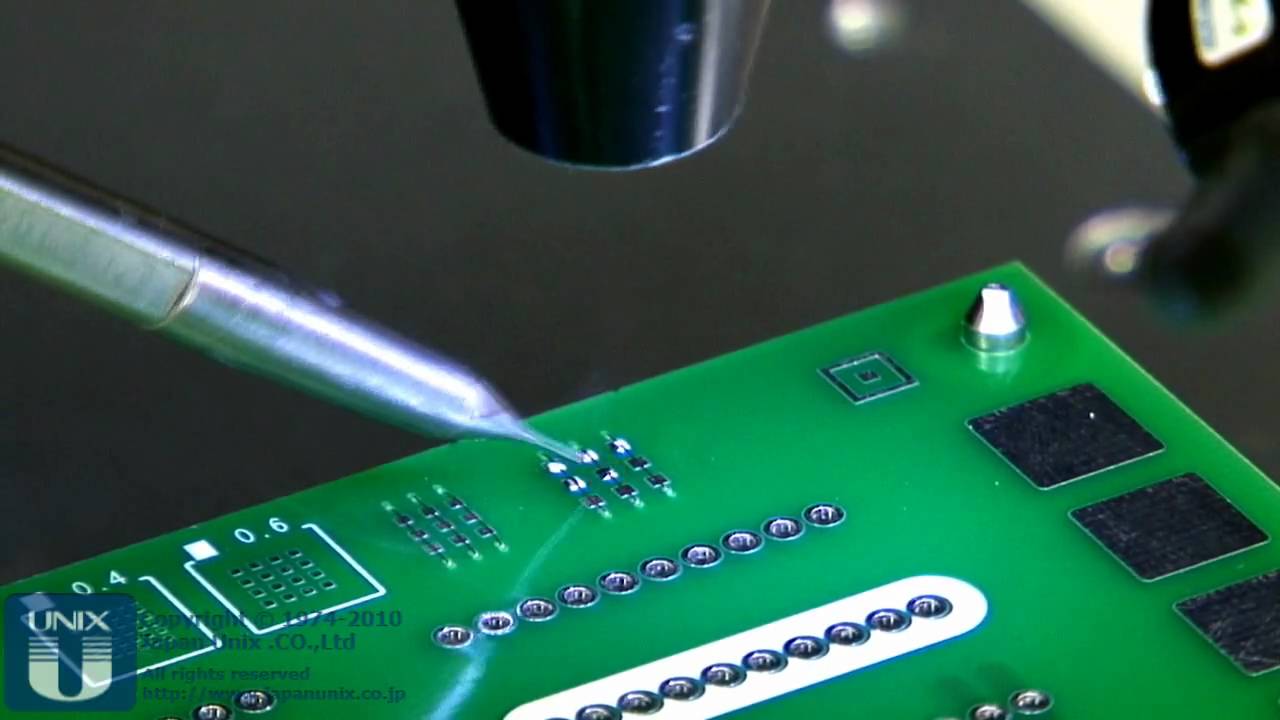
Laser soldering
Laser soldering Magnetic wire
Video of high speed soldering placement using a laser head.
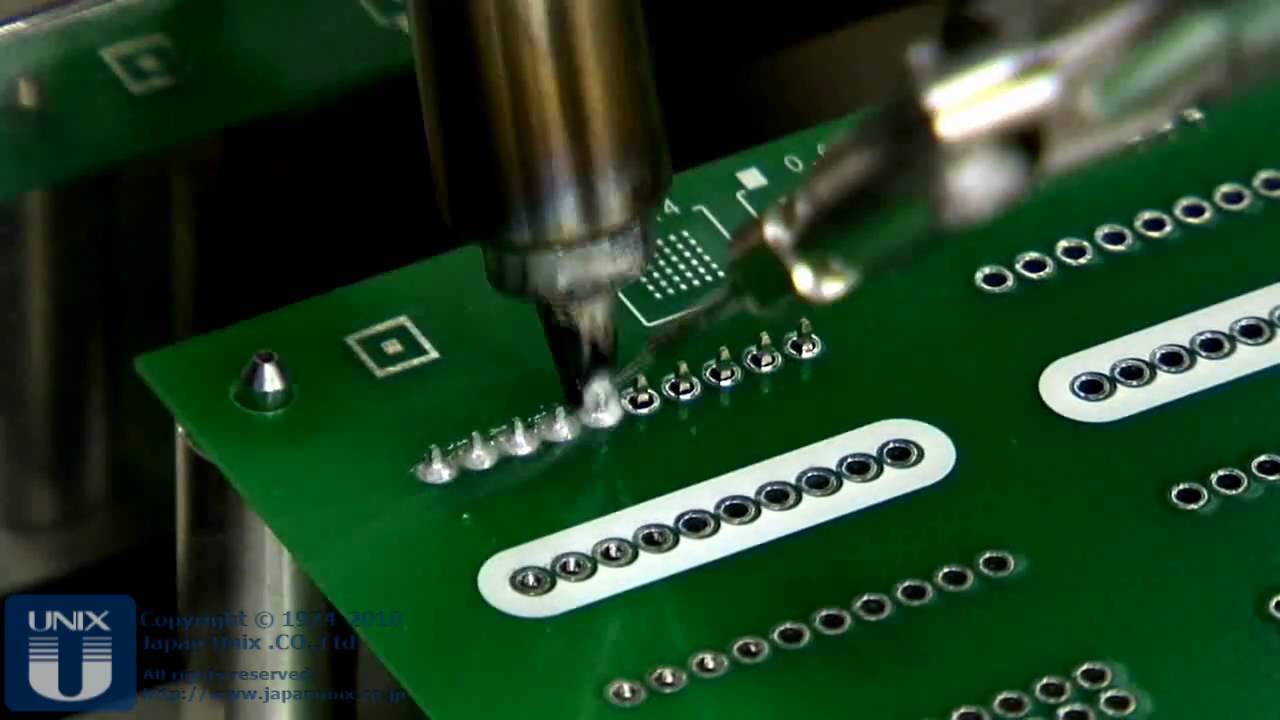
Robotic soldering
Automatic soldering robot High speed point solder
Point soldering that is also a basic. High-speed and reliable soldering installation by a specialized robot
– Why is the temperature so important? Laser soldering mechanism –
The solder’s composition status changes depending on the rising or falling temperature conditions, and optimal strength and reliability cannot be realized unless the temperature is appropriate. The fair temperature for soldering is a temperature in which the solder’s internal composition changes hardly at all from before it was heated. When excessive heat has been applied, both strength and reliability decrease due to composition changes. Flux also flows differently at different temperatures, and when heat is applied at the right temperature, the flux will at first flow to the solder position, and will remove the surrounding oxide skin and dirt, and will improve the solder’s tightness. The application of excessive heat will stop the flow of flux, instead making the solder flow first. Furthermore, excessive heat will damage the PCB and will create many problems such as board internal cracking that cannot be visually confirmed.
-The impossible becomes possible after understanding laser soldering principles –
The first main prerequisite for laser soldering is to use it with careful consideration about heat application conditions. It is actually an established technique, and depending on the way it is used and the application, it can replace some of the weaker areas of tip soldering to enable soldering that was previously impossible.
- Non-contact means it does not place a load on the PCB
- Efficient heat application and solder supply enables stable soldering automation
- It enables soldering in narrow confines on high-density board assembly.
- High maintainability
The most important characteristic of laser soldering is its non-contact soldering ability, and there is no contact at all with either the PCB or the component. There is no physical load placed on the PCB, only laser light and the solder supply. Laser’s great advantages are in its ability to efficiently apply pinpoint heat, to apply light to confined spaces where a tip cannot fit, and to handle tightly-spaced assemblies, by changing the light angle and taking other steps. Maintenance work can also be reduced
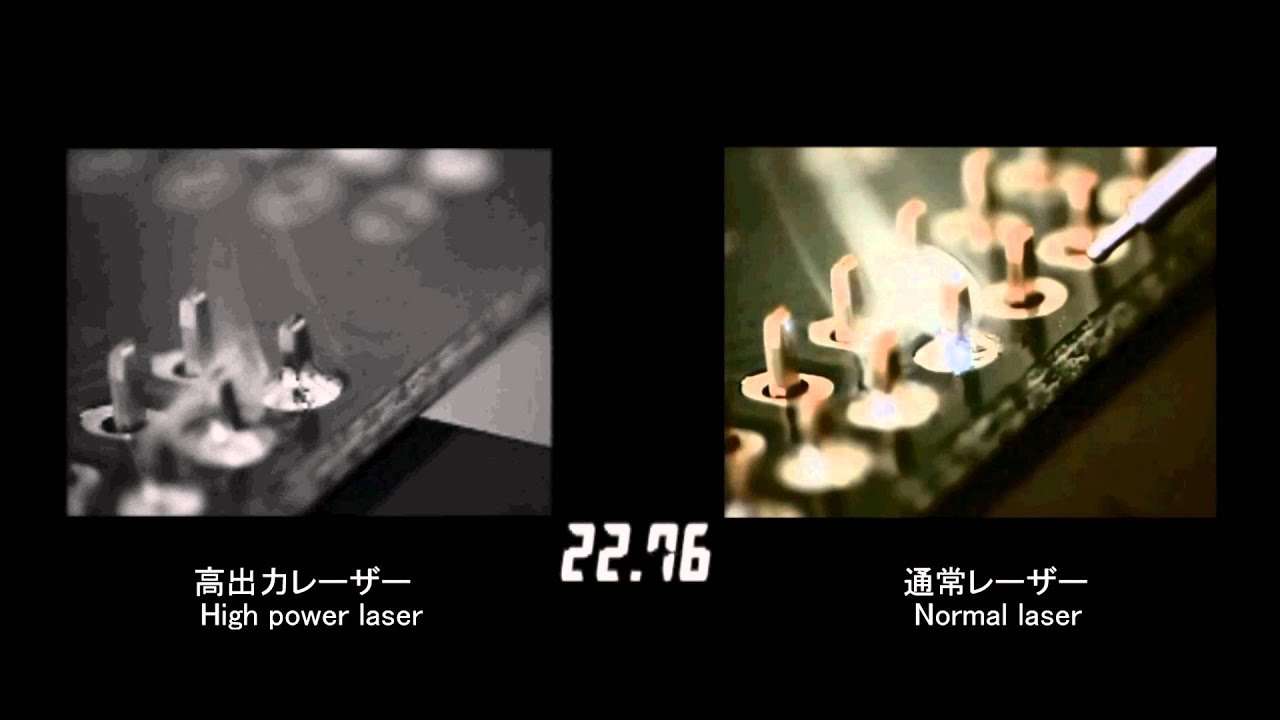
Robotic laser soldering
High output laser soldering robot
Speed comparison between high output laser and ordinary laser
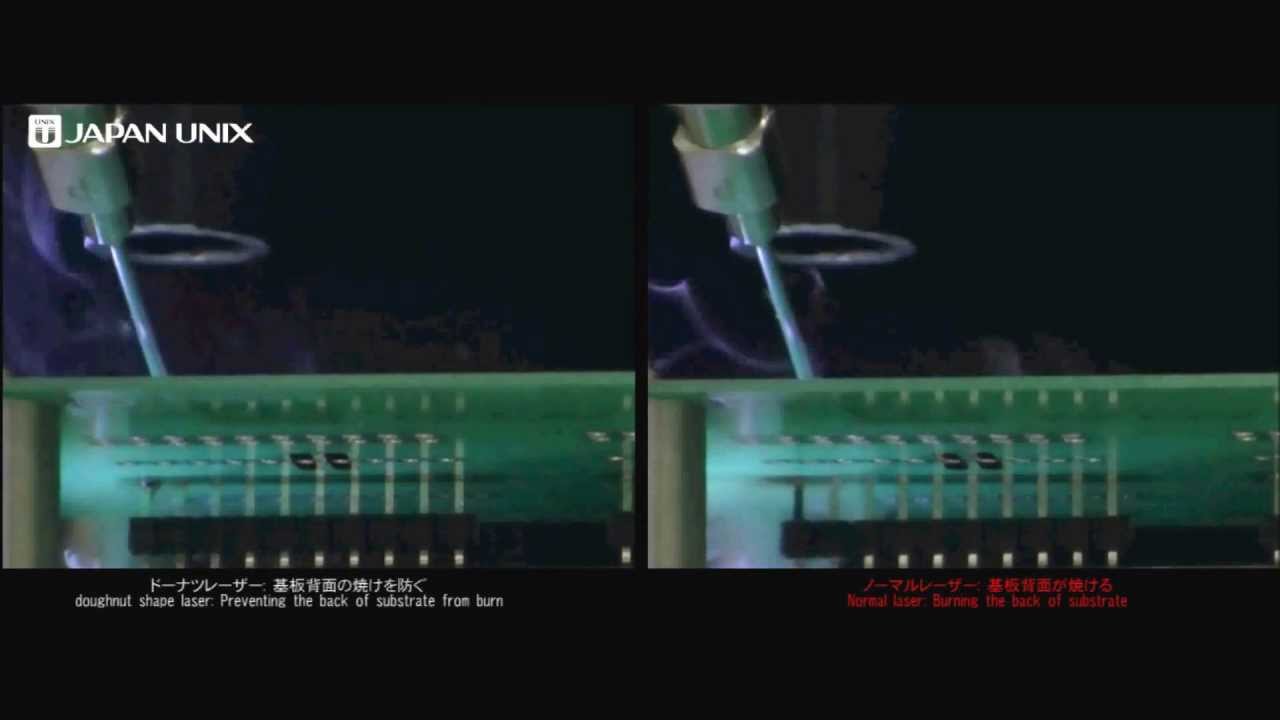
Robotic laser soldering
View of laser soldering light
Video of laser soldering assembly of very fine components
– Future advances and developments of laser soldering –
Japan Unix successfully commercialized a laser soldering system early on, just as we did with iron tip soldering. Furthermore, with a number of experiments, inspections, and evaluation trials, we have rigorously investigated the bond strength and reliability. Our extensive experience in systems introductions has let us establish application knowledge for laser soldering. We guarantee that customers can adopt these systems with confidence.
However, laser soldering is absolutely not just a replacement for contact soldering. It is important to distinguish the strong points of each and match them to the application.