Test Request Service
Identifying Issues in Establishing a Mass Production System
In order to establish a stable mass production system, it is necessary to identify potential problems in the production line and set soldering conditions. Japan Unix provides multidimensional testing to find optimal soldering conditions based on workpieces (prototypes) received from customers, using flexible implementation methods tailored to the customer’s needs.
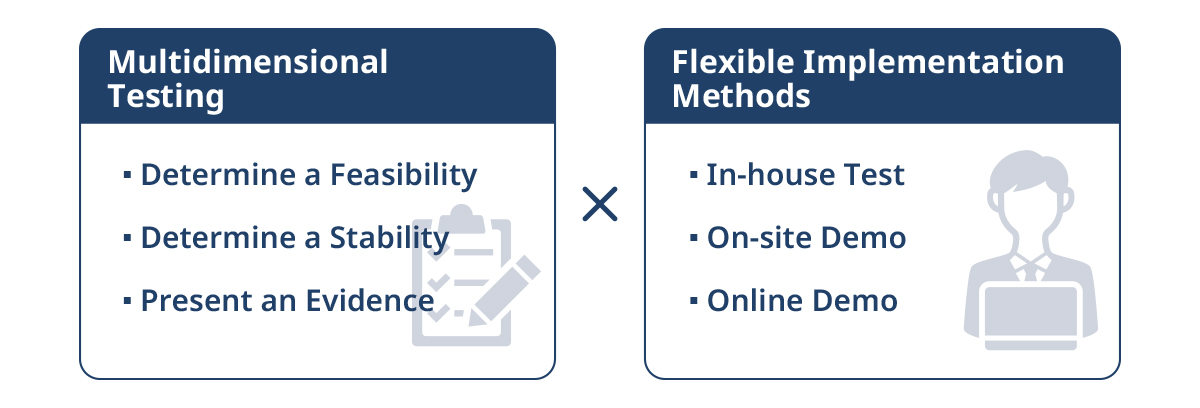
“Visualization” of the Soldering Process
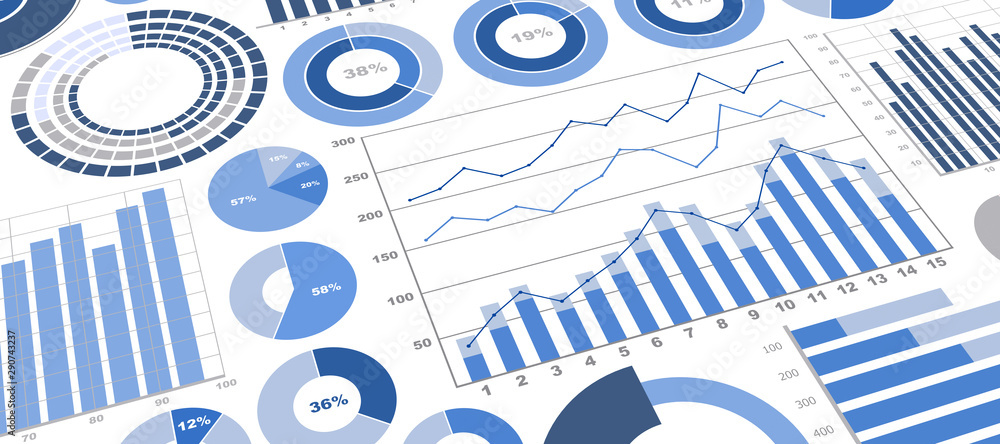
The purpose of Japan Unix’s soldering test is to “Build a Stable Mass Production system”.
In order to commercialize your workpieces and bring them to the market, it is essential to establish a stable mass production system without any uncertain and unpredictable elements. Therefore, we conduct tests to verify what method of soldering will ensure stable quality after the start of mass production and to establish “Optimal Soldering Conditions”.
In addition, the test not only presents the results, but also visualizes the soldering process and shares the process of setting the conditions. This allows the customer to be convinced of the appropriateness of the set conditions and the validity of the soldering process, and also leads to the discovery and analysis of uncertainties.
Multidimensional Testing
Based on our accumulated know-how and state-of-the-art soldering knowledge, Japan Unix provides multidimensional testing for determining feasibility and stability and presenting evidence. We also identify issues that have not yet become apparent and that may hinder the establishment of a mass production system.
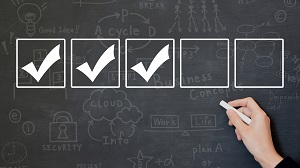
1. Determine a Feasibility
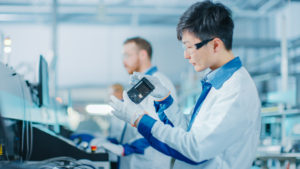
2. Determine a Stability
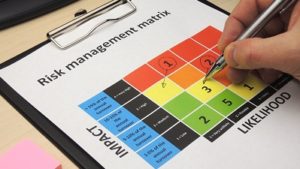
3. Present an Evidence
These three types of tests are not always conducted by us. We will select the necessary tests according to the timing of introduction and the conditions required by the client. In some cases, Japan Unix will perform the feasibility testing, the client will perform the stability testing, and later request us to provide evidence. If you request Japan Unix to perform the test, we will verify the appropriateness of the set conditions, validate the soldering process, and find and analyze uncertainties, all free of charge.
*When conducting tests, we recommend that you prepare 10 or more workpieces for evaluation of the optimum conditions. Please consider this service.
Flexible Implementation Methods
You can choose to conduct a test by “In-house Test,” “On-site Demo,” or “Online Demo,” depending on your situation and requirements. All testing methods are free of charge. For those who wish to conduct stability determination and evidence presentation tests, we recommend conducting the test in the form of an On-site or Online Demo.
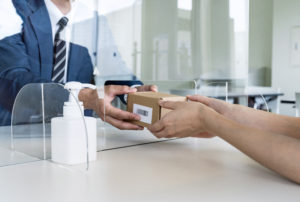
In-house Test
In the In-house Test, we receive workpieces from our clients, and our soldering engineers conduct multidimensional tests at our labo. After the test is completed, we select the necessary conditions for soldering, and our sales staff and engineers in charge will provide a thorough report on the process, results, and proposed issues with reports and video data.
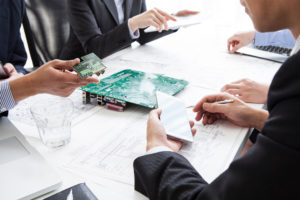
On-site Demo
In the On-site Demo, the client comes to our office to conduct a multidimensional test together with our soldering engineers. The client can ask any questions he or she may have on the spot, and the test pattern can be checked so that the process of selecting the conditions can be clearly understood. The On-site Demo is the best way to maintain quality and determine countermeasures against defects in mass production. In Japan, we can conduct tests at our labo in Tokyo, Osaka, and Nagoya. If you wish to conduct the demo overseas, please check with our local offices and overseas agents around the world
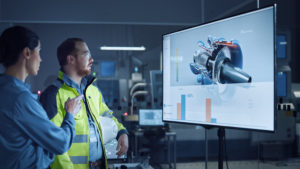
Online Demo
The online demo is a demo that you can participate in remotely. Through multiple cameras, management software, and microscope cameras, the soldering process can be closely monitored from a remote location. Since there is no need to visit our office, it is easy for your other department’s staff, superiors, and even people overseas to participate, and it is also a feature that allows all parties involved to share the condition selection process, including members of each domestic office and overseas production plant.