Global Support
Support for Global Line Starting-up & Defects
When Japanese companies set up production lines overseas, it is important to properly manage “QCD” (Quality, Cost, and Delivery). To achieve this, it is a prerequisite that the production line does not stop and that products are delivered on a “just-in-time” basis.
However, to manage production overseas, where language, culture, and environment are different, it is important to overcome such differences and communicate sincerely. Japan Unix understands the challenges of overseas production management and has put in place a support system to keep production lines running.
Establishment of a Three-tier Overseas Support System
Japan Unix has a three-tier overseas support system that includes local distributors, overseas offices, and the head office to maintain a stable mass production system even in foreign countries with different languages and cultures.
Local distributors are the first to respond to any problems that may arise, and they excel in speed. Overseas offices are capable of fully communicating and responding to complex issues that cannot be resolved by local distributors. The “Headquarters”, with its accumulated experience, knowledge, and know-how, including the latest technologies. We back up our clients with a three-tiered system that takes advantage of the features of each.
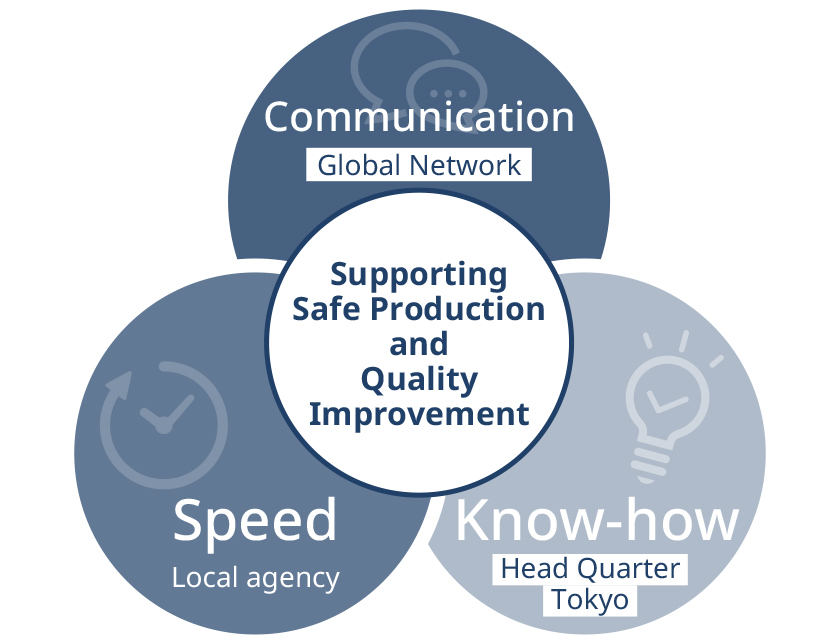
Local Distributors
When a problem occurs, an engineer from a local Japan Unix distributor first goes to the site to gather information. It is not uncommon for problems that occur at overseas factories to be caused by something other than the product itself, such as a change in materials or parts without permission. We usually build a good relationship with local engineers, and when a problem occurs, we gather information and investigate the cause. For this purpose, local engineers who can rush to the site immediately and communicate smoothly are the right people for the job.
Japan Unix Overseas Offices
Japan Unix’s overseas offices are staffed with engineers who have a thorough understanding of the local language, culture, and education. If the problem cannot be solved by the local distributor’s engineers alone, the problem is solved by the engineers at the overseas base, who also have sufficient knowledge and experience in soldering automation know-how, after receiving information sharing from the local distributor. Many defects can be resolved at this stage. In addition to handling problems, we can also provide engineer training and other services.
Japan Unix Headquarters
If there is a fundamental problem with the product that cannot be resolved at the overseas site, information is shared with the overseas site, and development and technical staff at the Japan Unix headquarters are assigned to resolve the problem. Although we are inferior to local distributors and overseas offices in terms of communication, our soldering engineers at the headquarters can respond directly to customers in English, German, Spanish, Chinese, and Korean. We can also propose solutions regarding issues of engineer training that go one step further and ongoing problems.
All for “Non-Stop Production”
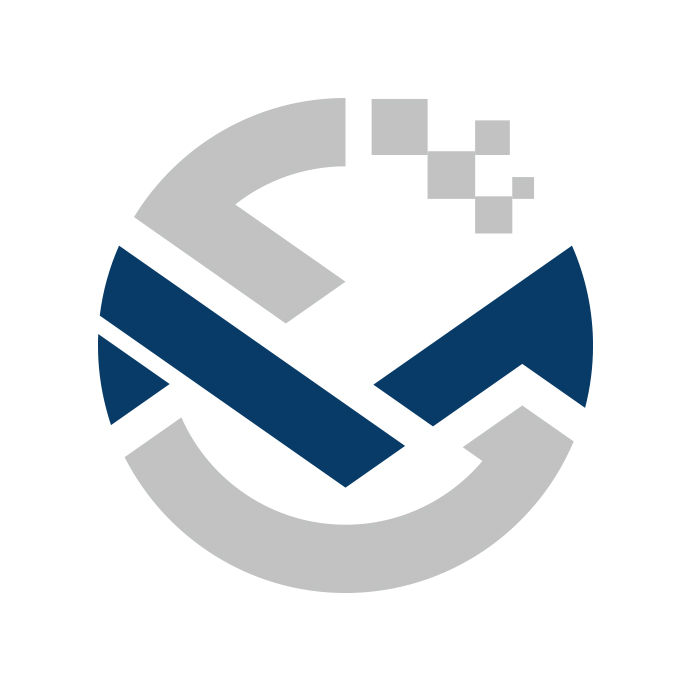
In addition, Japan Unix offers “Soldering Manager,” soldering robot management software. This software can be used to help solve problems by identifying and verbalizing the situation when defects occur.
Defect information handled by local distributors and overseas offices is also shared with the customer’s head office by creating a report on the process from problem occurrence to resolution. If necessary, we also conduct reproducible verification experiments tailored to the on-site environment by sending samples to Japan in order to determine the cause of defects after mass production. As soldering experts, we will do our utmost to support our customers’ nonstop production.