TOYOTA MOTOR CORPORATION
Toyota Motor Corporation adopts IPC for standards of Soldering visible Quality
New technology standards with IPC added to internal standards for further global expansion
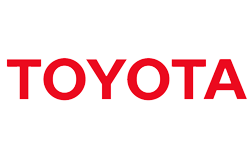
Toyota Motor Corporation officially adopted IPC, an international quality standard for solder and mounting technology, for solder appearance standards in the newly created Toyota Standards (TS) in 2021. The company has created a new solder appearance standard with IPC at its core, replacing the previous in-house standard. We interviewed a person in charge of the Control Electronics System Development Department about the purpose, background, and aims of the project.
Company Name | TOYOTA MOTOR CORPORATION |
---|---|
Founded | August 28th, 1937 |
Gross Sales | 29.93 trillion yen (FY2020) |
Number of employees | 74,132 (consolidated 359,542) |
Business | Production and sales of automobiles |
To learn more, click here to download the PDF file.
How IPC was adopted as an internal standard
Toyota Motor Corporation
Electronics Control System Development Div.
Development Process & Quality Innovation Dept.
Mr. Masahiro Ishikawa
Electronic Performance Development & Engineering Dept.
Mr. Hisao Nishimori
Would you introduce about your roles in the company?
We, both of us belong to design and development division in Toyota. The Development Process & Quality Innovation Department is taking care of overall design quality and in charge of determining the standard of soldering visual quality of electric and electronic components. The Electronic Performance Development & Engineering Department is in charge of developing some electronic performance in the vehicle, and one of them is a test method of “Durability Test for Solder Joint”. On the other hand, the “Soldering Production Quality” is controlled by the Quality Assurance division. We would like to talk about the “visual criteria affecting the Standard of Soldering visible Quality”, that is managed with design and evaluation point of view.
How did you ensure the soldering quality before?
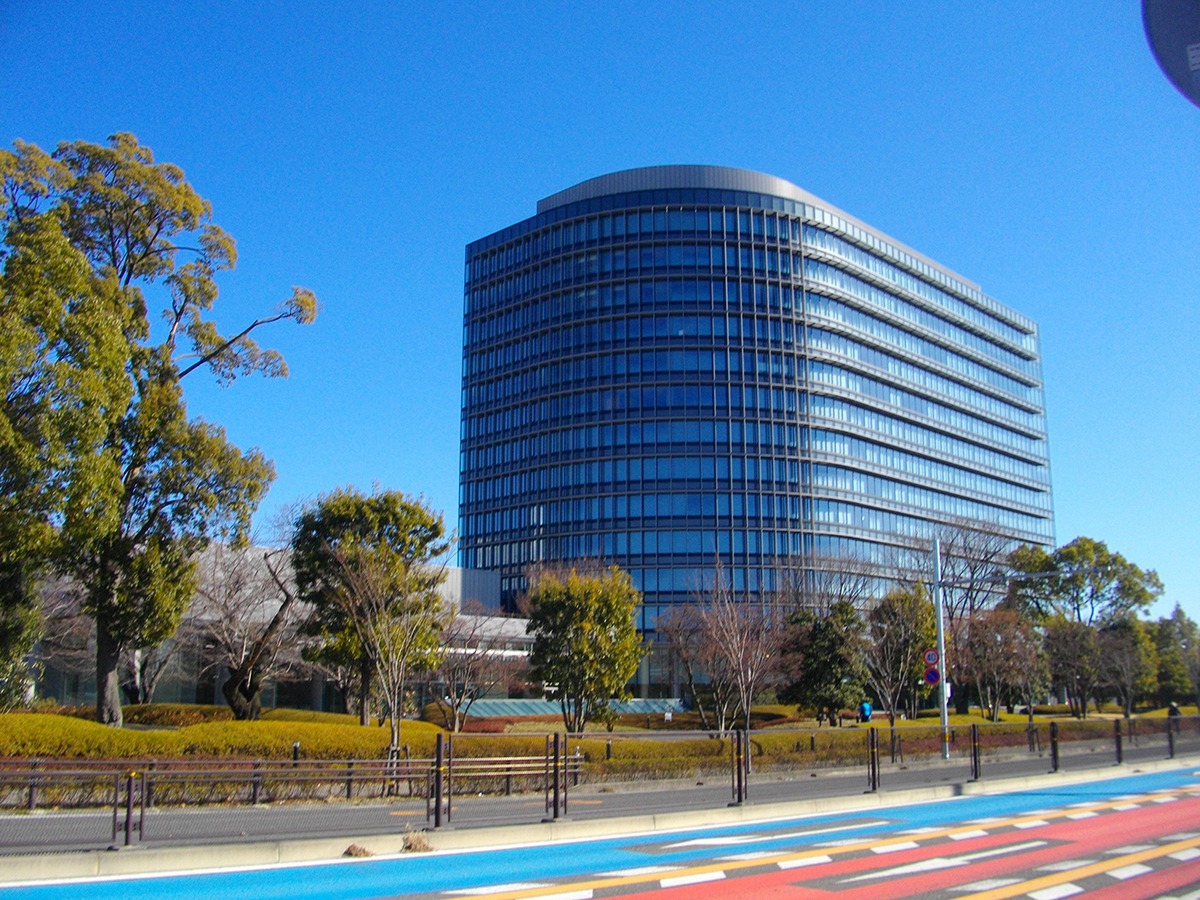
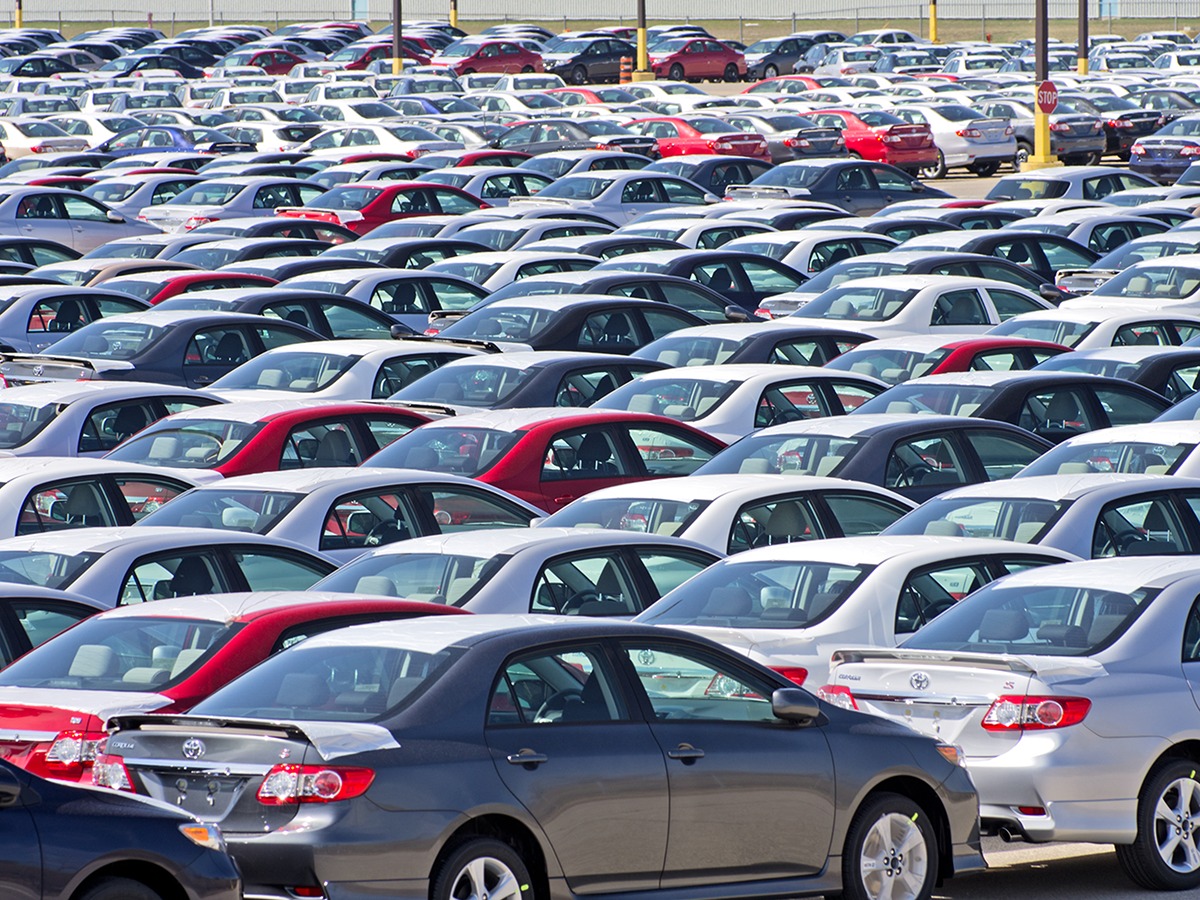
In Toyota, we recognize that soldering and its quality are the key reliability factor, and we have been established and maintained Toyota’s original quality standards for more than 30 years. We have ensured the soldering reliability and design quality while revising those standards year by year.
Toyota issues required design quality specifications to suppliers, and suppliers develop and deliver products based on our requirements. And then, the Quality Assurance Department of Toyota headquarters/manufacturing sites ensure the soldering production process and quality at each supplier plants. In order to secure soldering quality, Toyota think about two pillars which are the design quality and the production quality, and Toyota achieved total soldering quality with those two pillars.
However, due to globalization, our supply chain also expanded with overseas suppliers, and we faced a significant gap with new suppliers, especially Production Assurance and Quality Control Department at factories were advised like “We cannot disclose items and criteria that Toyota does not require”.
Therefore, we have been discussing with Quality Assurance Department to change the process of working procedures since 2010. As spoked earlier, Toyota provides required specifications to our suppliers from our design divisions. In that process, we changed our process that “In addition to the soldering reliability requirement, Toyota requires its visual (appearance) standards at the same time.”
What were the criteria you established at that time?
Toyota had in house electronics product and assembly lines; thus, the initial Toyota Standards were referred to JIS, IPC and the internal standard which was used at that plant. However, when releasing the initial standards, many suppliers asked us that “So, how is this Toyota Standards relevant to IPC?”. Then, we recognized IPC had become the substantial standard in the global automotive industry, and we began to study and started considering the new revision referring with IPC-A-610.
We had a policy that Toyota is going to adopt common standard in the world, and according to the issues of J-STD-001 / IPC-A-610 Automotive Addendum, we launched new Toyota Standards of soldering visual quality, which was referred to IPC standards in Feb 2021.
New Solder Appearance Standards Incorporating IPC Welcome from Suppliers
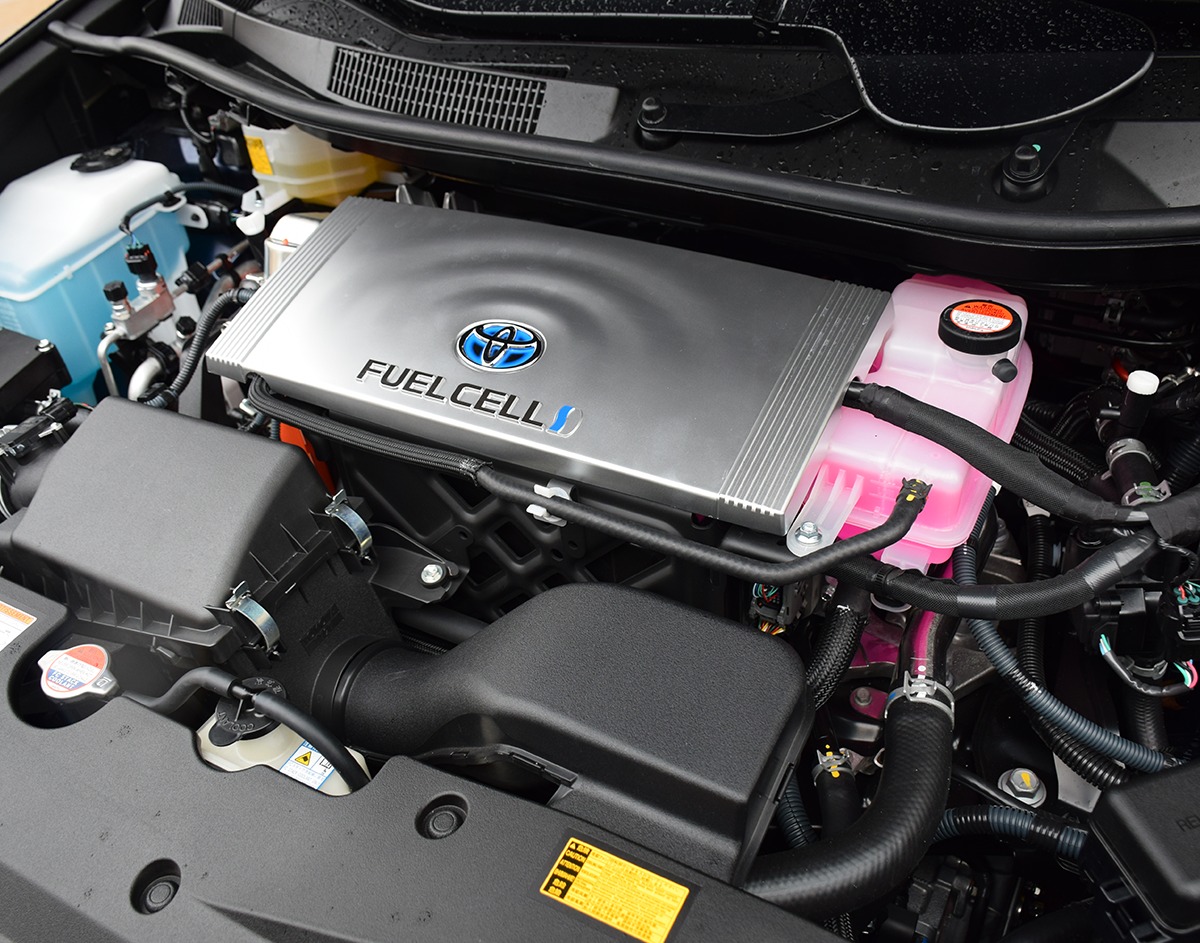
With the automotive industry undergoing a period of change, why did you choose IPC?
For some time now, solder appearance standards have been perceived quite differently, even with similar content and conditions, depending on whether they are IPC-based, based on Toyota’s in-house production, or JIS. It was also significant that the IEC was also based on the IPC.
What has been the reaction to the introduction of the IPC, both internally and externally, as well as from overseas offices?
Aiming to Realize Soldering Durability and Efficient Quality Control with the New Technical Standards
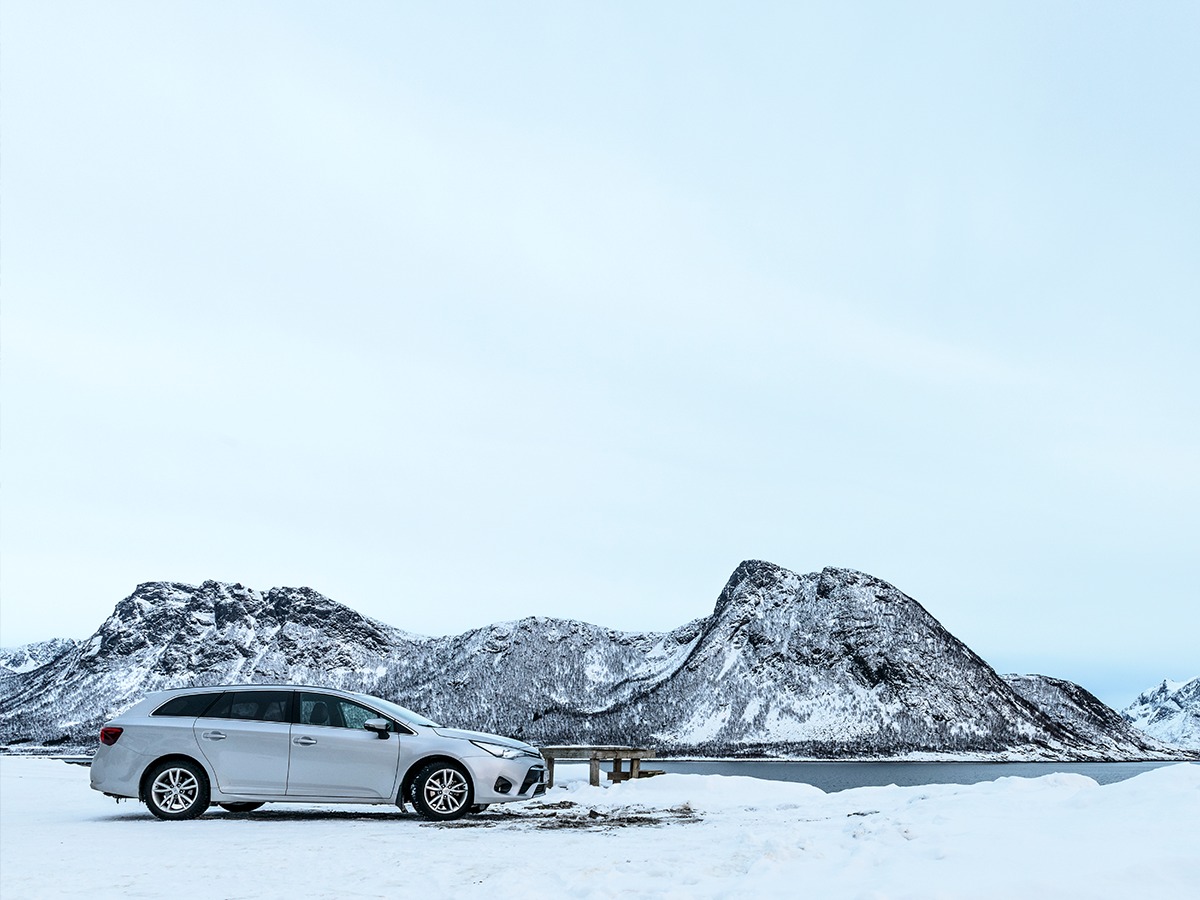
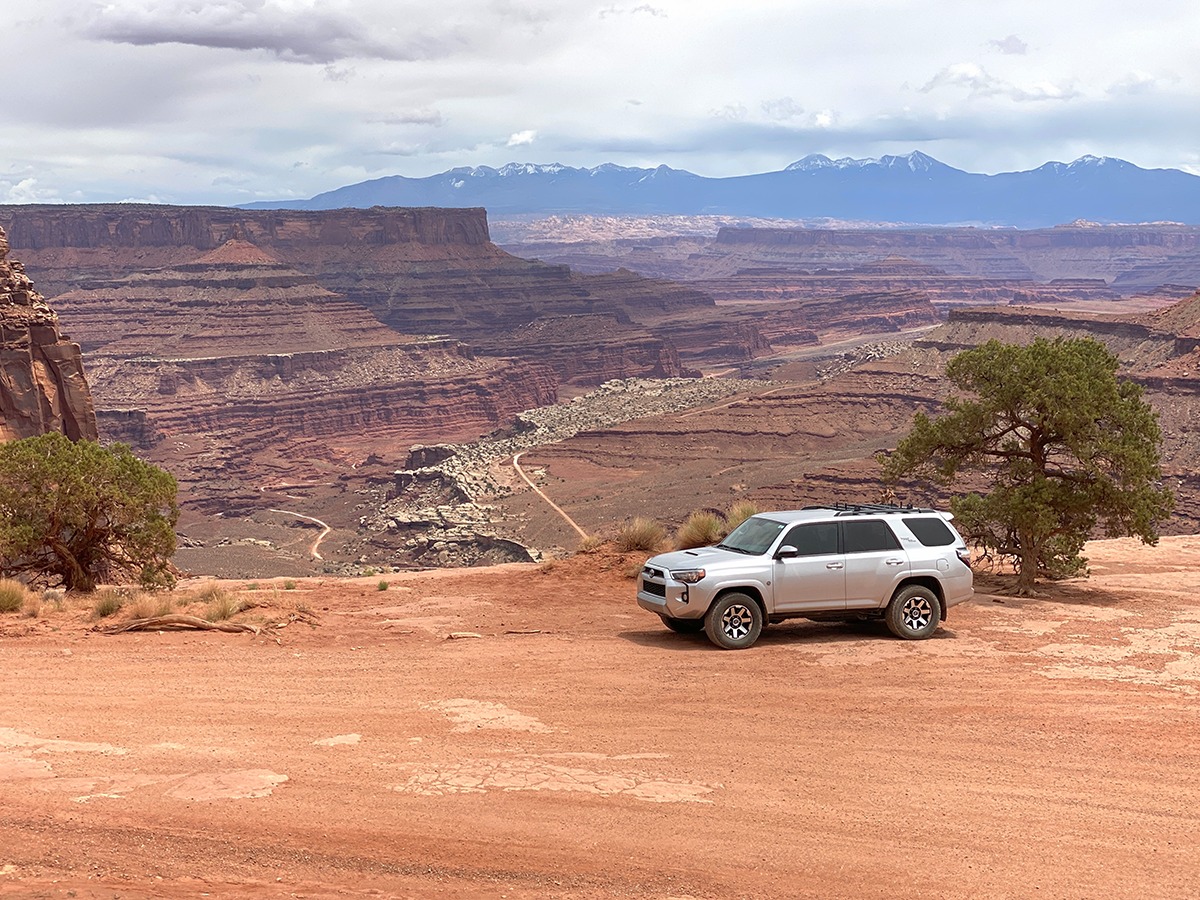
What were the differences/gaps between Toyota’s quality requirements and IPC’s requirements?
For example, in IPC requirements, solder balls are acceptable if they are entrapped, encapsulated, or attached. However, automobiles are expected to use for a prolonged period in various harsh environment such as extremely freezing weather and hot/humid conditions.
Even though those solder balls are entrapped, encapsulated, or attached in the coating material, the coating alone cannot guarantee the stability over the end of the vehicle’s life. For covering and supporting those IPC requirements, we added supplemental description to Toyota’s Technical Standards, such as what would happen if those entrapment, encapsulation, or attachment are loosen. In case that the standard just says “Acceptable, if solder balls are fixed (entrapped/encapsulated/attached) at the initial stage of soldering process”, then the idea will be resulted in obtaining a pass/fail status by just making a checklist and marked or unmarked the items. To prevent this situation, we continue to communicate and discuss with our suppliers as usual, to achieve a product quality goal that must be guaranteed.
In regard to this newly developed Quality Standards, what are you expecting from your domestic and overseas suppliers?
For global suppliers, Toyota requires its own standards, and other OEMs may require IPC standards. We believe that there was a troublesome tasks and efforts due to these two (2) different standards. By adopting IPC into Toyota in our TS, we hope all suppliers will be able to control their soldering quality efficiently.
In addition, due to the once-in-a-century transformation in the automotive industry and efforts for CASE technologies, Toyota will be more likely to interact and deal with new suppliers than ever before. In such cases, by utilizing IPC as a Common Language, we expect that soldering quality control can be performed by both of we and supplier at an earlier stage and more efficiently.
In new Era that Changes with CASE Technologies, Building New Relationships with Suppliers Utilizing IPC as a Common Language
There are still many companies in Japan that are unfamiliar with IPC. Would you please summarize today’s discussion and give advice and messages for those companies?
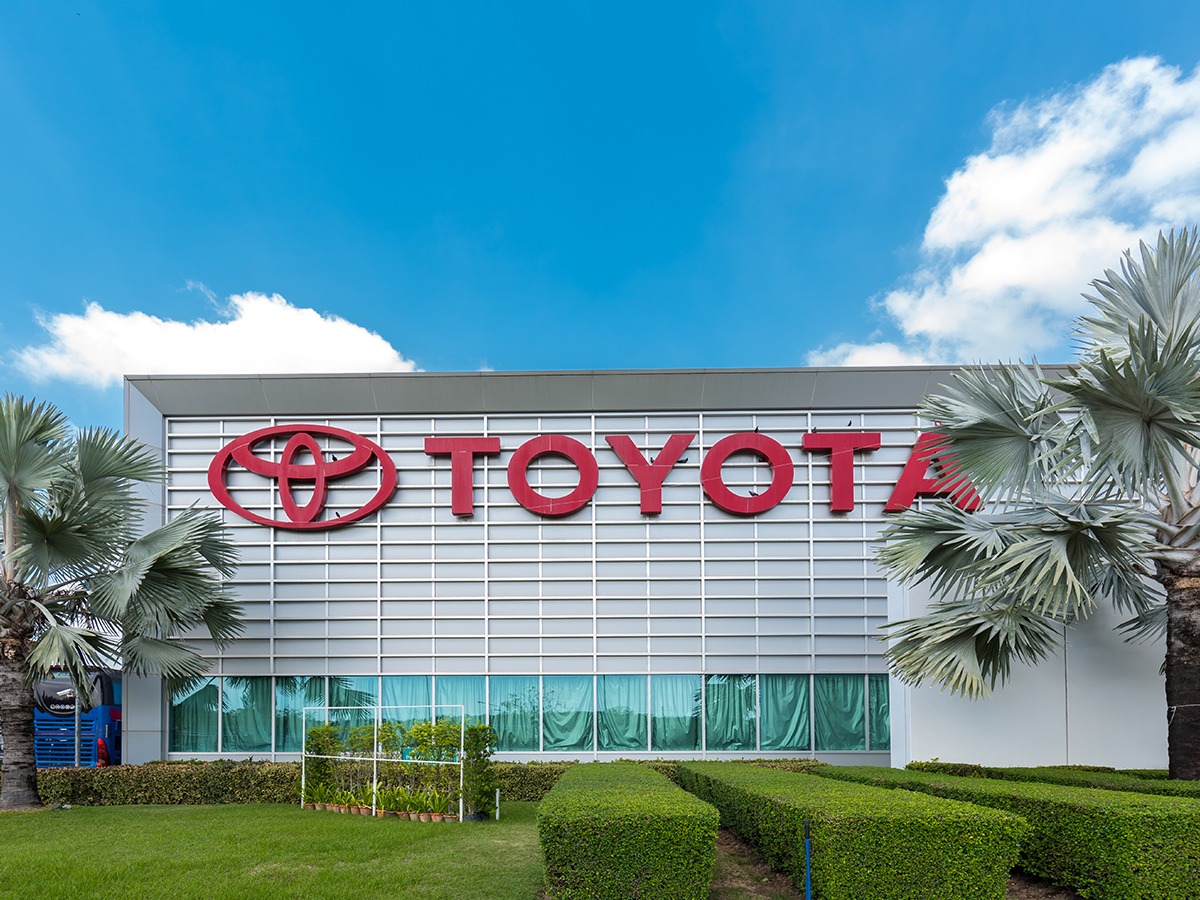
When we deployed Toyota’s internal standards/criteria to suppliers, we were often asked about the relationship with IPC standards. We have been approved suppliers who manufactures semiconductors and/or devices for automotive use. By adopting IPC this time, suppliers will be able to efficiently verify and assure their manufacturing quality at the global level. As a result, we hope to build a “Win-win relationship” with suppliers.
Since we are in a period of once-in-a-century transformation and in the time of “CASE”, It would not be enough just to rely on the past knowledges and experiences. We would like to be a teammate of IPC’s global network so that we will be able to implement various technologies on Toyota vehicles, while incorporating the latest information
To learn more, click here to download the PDF file.