Basic Knowledge of Soldering Technology Vol.3 “Ultrasonic Soldering
Ultrasonic soldering can bond non-metals such as solder and glass. It is also an environmentally friendly process that can remove oxide film from aluminum and stainless steel without the use of strong flux.
Attention-grabbing process that can solder to glass
Ultrasonic soldering is a remarkable process that can join solder and non-metals. An ultrasonic wave of approximately 60 KHz is emitted from a soldering tip heated by a heater. The pressure difference in amplitude generates a small bubble-like cavity (cavitation effect) in the solder melted by the heat, and the energy of the cavitation when it collapses is used to make the joint. The bonding principle of ultrasonic soldering varies depending on whether the base material is metal or non-metal.
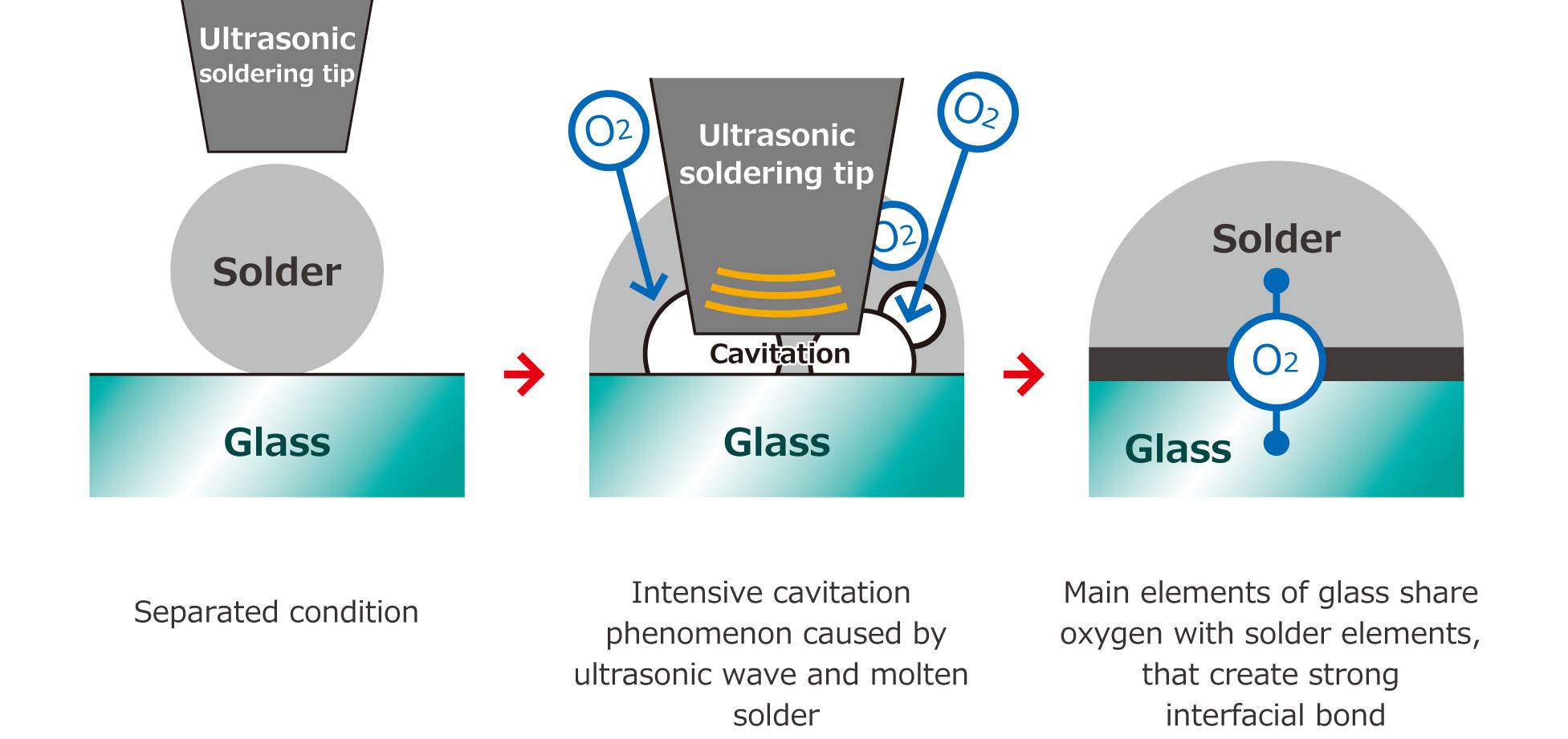
Metallic
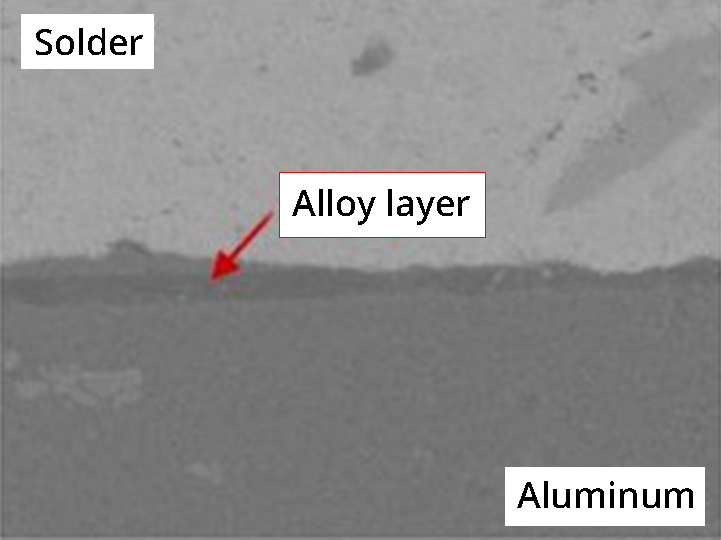
Soldering is performed by removing oxide film on the surface of metals such as aluminum and stainless steel without using flux (soldering accelerator) by the energy generated when cavitation ruptures.
Antimetallic
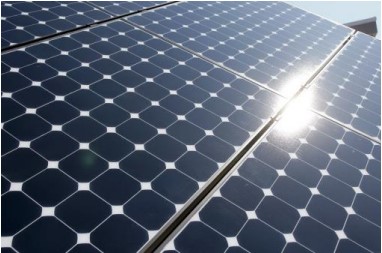
Glass and ceramics cannot be soldered without removing the oxide film because the material itself is an oxide. Therefore, the bursting energy of cavitation is used to remove the air layer, organic matter, and foreign objects from the bonding surface. Subsequently, it is believed that oxygen mediates the covalent bonding between the oxide, the base material, and the metallic elements of the solder, thus completing the soldering process.
Features of Ultrasonic Soldering
(1) Flux-free soldering is possible with metal-to-metal
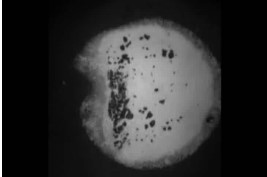
(2) Capable of soldering to non-metals
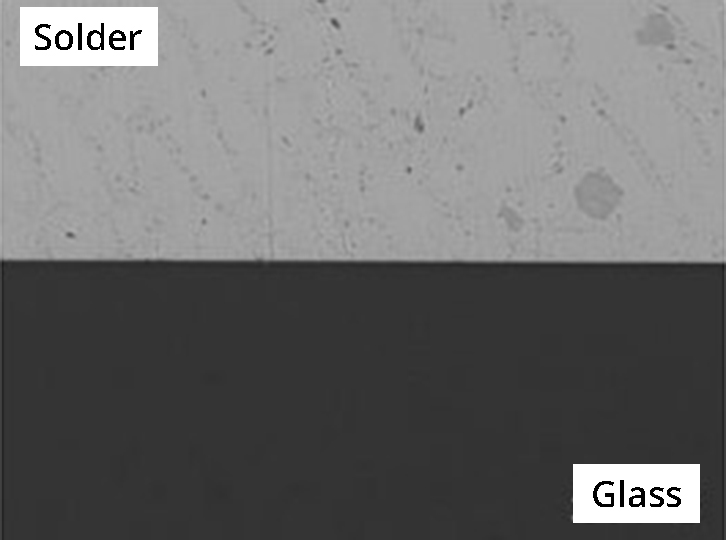
Conventional soldering is essentially a joining of solder and metal. Ultrasonic soldering can join solder to non-metals such as glass and ceramics.
(3) Expanding applications
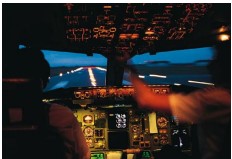
Ultrasonic soldering is being used in a wide variety of situations, starting with bonding electrodes to the glass surface of solar panels. The MCU (microcontroller unit), the brain of an automobile, is housed inside an all-aluminum housing, where soldering is sometimes performed using ultrasonic waves. Also, in recent years, in order to reduce weight and cost, aluminum wire is increasingly used for motor coils and transformers, including aircraft instruments, instead of copper wire. Ultrasonic soldering is also playing an active role in such soldering situations.
Select the method that best suits your purpose.
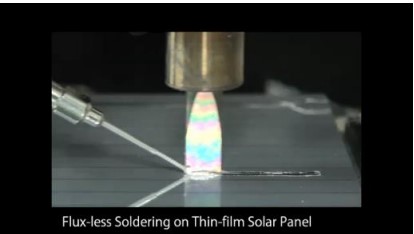
With the advent of new methods and technological advances such as ultrasonic waves and lasers, the scope of soldering has expanded from minute objects to objects with large current flow, and even to materials that were previously impossible. It is required to understand the characteristics and strengths of each soldering method and then select the most appropriate method according to the purpose and application.
To learn more about the coupling principle of “ultrasonic soldering,” its expanding applications, and Japan Unix’s soldering units, please click here to download the PDF file.