General Motors(GM)
Why IPC for Enhanced Quality in Automotive Electronics?
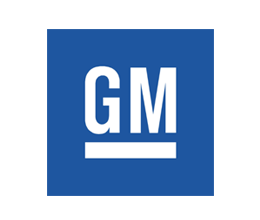
General Motors (GM) has been in the Chinese market for more than 90 years and currently has 14 companies, including 11 Chinese joint ventures and three wholly owned affiliates, with more than 58,000 employees. Buick,In 2016, GMand its affiliates shipped a new record 3,870,587 vehicles in China. GM’s vehicle shipments in China helped the company maintain its market share lead in the country for the fifth consecutive year.
This article was conducted by IPC Asia Pacific and GM China, and translated and published by Japan Unix, Inc. with the approval of GM World Headquarters.
To learn more, click here to download the PDF file.
1. How did you incorporate IPC standards?
The automotive industry requires a very high level of reliability and does not tolerate any issues that may pose a safety concern. To ensure safety and security, GM has introduced the IPC as an audit standard for lead-free soldering processes, applying the CQI-17 (AIAG) to several suppliers of critical components.
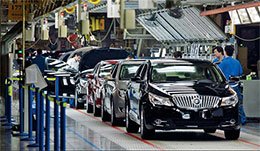
2. How is it applied in supplier quality audit management?
Factories that handle printed circuit board assemblies (PCBAs) conduct self-audits according to the requirements of CQI-17. Primary (Tier 1) component manufacturers also annually audit their respective PCBA suppliers, auditing them according to the requirements of CQI-17 again. The importance of the role of the IPC standard stands out in this process. In particular, the increasing prevalence and application of IPC-A-610 on a global scale has led to significant improvements in the management of soldering defects in electronic assemblies, even among suppliers. Many decisions that are difficult to quantify can be found by referring to the IPC-A-610. It is like an encyclopedia or dictionary for the electronic assembly industry.IPC training programs can be implemented anywhere with the same quality and content, and are very effective in providing a basic understanding of standards and the fundamentals of quality judgment. By introducing IPC training, GMs are able to focus more directly on individual requirements and differences between IPC and GM standards, thereby reducing execution time and improving efficiency.
3. What has been achieved by applying the IPC standard?
We believe the following two benefits have been realized. First and foremost, it has greatly facilitated communication among internal staff. Second, it has been easier for our suppliers to understand and comply with our requirements and instructions.Being able to provide clearer and more specific requirements and instructions to suppliers has made it easier for them to understand and comply. As a result, administrative costs on the supplier side are reduced, which is very beneficial for a quicker response.
4. Advice for companies implementing IPC standards
The IPC standards are very easy to understand, with detailed explanations of requirements using pictures, diagrams, and plain text. the IPC standards are practical, good operating rules that are very effective and helpful in providing accurate requirements and guidance to the work groups. the IPC standards have a great impact on process productivity, quality uniformity, business development, I hope more companies will take advantage of the IPC standards and reap the benefits.
5. Requests regarding IPC standard requirements
We look forward to IPC continually updating the standards it has already published and, at the same time, publishing further technical standards that will be approved by the automotive industry for advancement in the industry. And we are very hopeful that IPC will develop a consulting program of certification courses and audits that will help the automotive industry move forward.
To learn more, click here to download the PDF file.