Celestica Japan KK
From NEC Miyagi to Foreign EMS.
IPC standard that became the core of the organizational change
Transition from the old system, which was mainly manufacturing for specific customers in Japan, to contract manufacturing for a wide variety of products in the global market
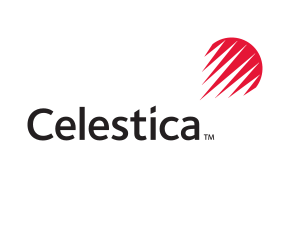
Company Name | Celestica Japan K.K. (formerly NEC Miyagi) |
---|---|
Founded | 2002(Japan), 1994(Global) |
Gross Sales | 56 million USD |
Number of employees | Approx. 25,000 |
Business | Contract manufacturing services for electronic equipment. The company undertakes the manufacture of products for businesses, and is particularly strong in telecommunications equipment. In addition to manufacturing, the company can also undertake everything from design to repair on behalf of manufacturers. In recent years, production of high-mix, low-volume, value-added products requiring high quality, such as aerospace and defense equipment, industrial equipment, energy equipment, healthcare equipment, and semiconductor manufacturing equipment, has increased. |
To learn more, click here to download the PDF file.
MBO from IBM; establishment of Japanese subsidiary through acquisition of NEC Miyagi and Yamanashi
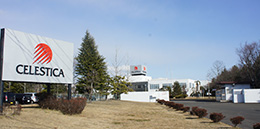
Please give us an overview of your company.
We are an EMS company based in Canada, founded in 1994. The company was originally IBM’s Canadian plant, and the management team at the time launched an MBO. This was at a time when the EMS business was just beginning to emerge around the world.
Celestica Japan was started when Celestica acquired NEC Miyagi and NEC Yamanashi, which were NEC’s communication systems development and manufacturing bases. Today, Celestica Japan manufactures optical transmission equipment and station equipment for domestic telecommunications carriers as well as telecommunications equipment for NEC and other major Japanese and foreign manufacturers. Like its headquarters, NEC Miyagi also focuses on diversified product markets, such as operation panels for disaster prevention radios, semiconductor manufacturing equipment, and ultra-precision printed circuit boards for satellites.
From the NEC era to an international standardization system with an eye on the global market.
IPC has been introduced in EMS around the world as a matter of course since 2002.
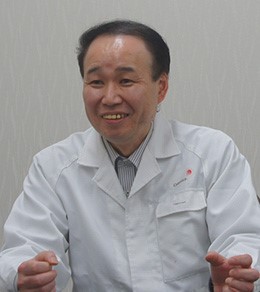
IPC-A-610 Mr. Tatsuya Chiba, MIT
How did you start working on the IPC?
It all started around 2000, when I was at NEC Miyagi, when the management at that time instructed me to study overseas standards. At that time, M&As among companies were flourishing overseas, and industry restructuring was active.
The electronics industry was still healthy in Japan, but it was a time when things were beginning to change gradually. In order to cope with the uncertain times, the management team was promoting management reforms, such as using overseas EMS to improve efficiency and strengthening the EMS business by taking on manufacturing contracts from all kinds of companies, both domestic and overseas, themselves.
I was surprised to hear that you had adopted IPC during your time at NEC. I had thought that IPC was introduced only after Celestica.
That’s right. I think the management at that time had foresight; during my time at NEC, we were like a factory specializing in manufacturing products for major domestic telecommunications carriers. However, I remember being told, ‘In the future, that alone will be a major management risk, and we will have to take work from other companies as well. After being instructed by my boss, I started by researching what standards existed in the world. As I researched major overseas EMS companies such as Celestica, Solectron (now Flextronics), and Foxconn, I learned that they had adopted IPC as a matter of course.
Combination of domestic original standards and international standards. Gradually conform to international standards through comparison of in-house standards and IPC.
What were the company’s own standards at the time?
At that time, the largest customer was the largest telecommunications carrier in Japan, which first had its own transmission standards. The customer had its own transmission standards, which we had milled into our own standards. After the introduction of IPC, we compared the in-house standards with IPC, identified areas that matched and areas that did not, clarified the criteria for each, and made the in-house standards conform to the IPC standards. Even now, we use the transmission standards of our client carriers, our own standards, and IPC in combination.
In-house standards and domestic standards will not be understood in the world.
IPC is the only reason why we can do business globally in Miyagi.
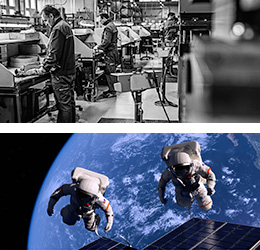
What are the advantages of using IPC?
Upon the acquisition in 2002, there was a factory inspection by Celestica. They were considering acquiring several other plants in addition to ours, but in the end they decided on us and NEC Yamanashi. I think it was largely because we had already introduced IPC at that time, so we understood what Celestica was looking for. If we had not even known about IPC, we might not be here today.
EMS also receives work from a wide variety of clients, and not just telecommunications equipment. IPC is a standard for mounting electronic components and is like a standard for EMS. The fact that we are now able to respond to customers in any field is a big advantage.
There is another big thing.
IPC is the reason why a company based in Miyagi Prefecture, can continue to do business on the world stage. For example, the number of people applying for employment has changed dramatically compared to when we were at NEC Miyagi. Recently, however, we have seen an increase in the number of proactive people who want to work globally in Miyagi without having to go to Tokyo. I feel that it is very significant to have a foundation that allows us to do business with the world without having to leave the region.
A common challenge for EMS is that ‘different customers have different requirements.
Adopting IPC and reducing manufacturing costs through standardized production methods/h2>
How are you actually using IPC?
I use the original documents as they are. When I am not sure about a decision, I look at the original IPC and make a decision.
The difficult thing about EMS is that different clients have different requirements. So it would take time, effort, and cost a lot of money if we had to interpret client standards and create all of our own standards for each product we manufacture. In this respect, IPC is highly versatile and can meet most clients’ requirements. It is versatile and helpful.
The IPC is easy for anyone to read, with detailed illustrations and photographic diagrams and explanations. By using the IPC together with in-house standards, you will be able to accurately and quickly determine good/failure.
Japanese companies tend to create their own standards and avoid standard parts. There is a tendency to believe that proprietary standards and custom-made parts create high added value and differentiation. However, if they use standard components, adopt international standards such as IPC, and become accustomed to using standard construction methods, they can lower their costs even more than they do now. Value-added and competitiveness should be focused on core parts and functions in the product.
To learn more, click here to download the PDF file.