Case Study Interview Lumileds: Advancing Manufacturing – From Innovation to Smart Factory Leadership
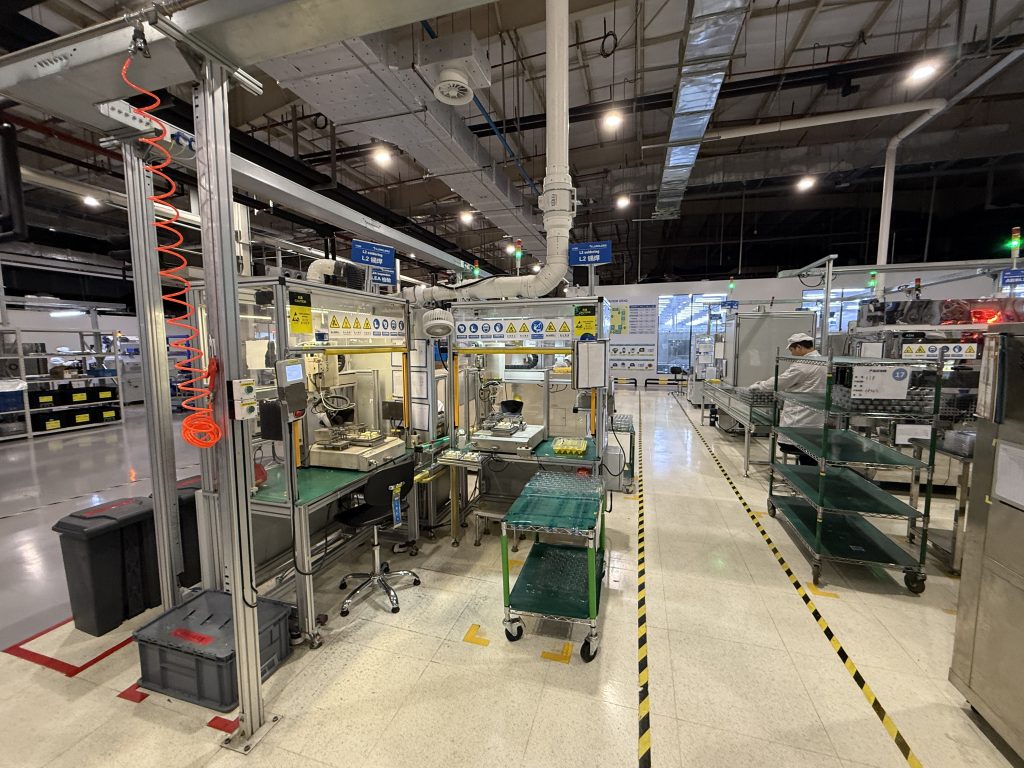
Case Study Interview
Lumileds: Advancing Manufacturing – From Innovation to Smart Factory Leadership
In modern manufacturing, the application of automation technology is bringing significant transformation to production lines. Particularly in the electronics industry, achieving a highly precise and efficient soldering process is key to maintaining competitiveness. As a pioneer in industrial soldering technology, Japan Unix is committed to providing advanced soldering solutions to its customers. This time, we interviewed the engineering team at Lumileds, a global supplier of optical and lighting solutions, to discuss the challenges they face in their production environment and the groundbreaking process improvements they achieved by implementing Japan Unix’s automated soldering technology.
Table of Contents
- Pursuing Excellence at Lumileds
- From Tradition to Smart Manufacturing: The Evolution of Lumileds
- The Limitations of Traditional Soldering Technology: Identified Challenges
- Eliminating Production Bottlenecks Through Automation
- From Needs Analysis to Solution Development
- Implementation Process: From Trial Operations to Full Deployment
- Notable Achievements: A Dramatic Increase in Productivity
- Japan Unix’s Laser Soldering
- Future Prospects: The Smart Factory Revolution Led by Laser Soldering
- Industry Insights: Opportunities Brought by Automation
- Related Content & Services
Pursuing Excellence at Lumileds
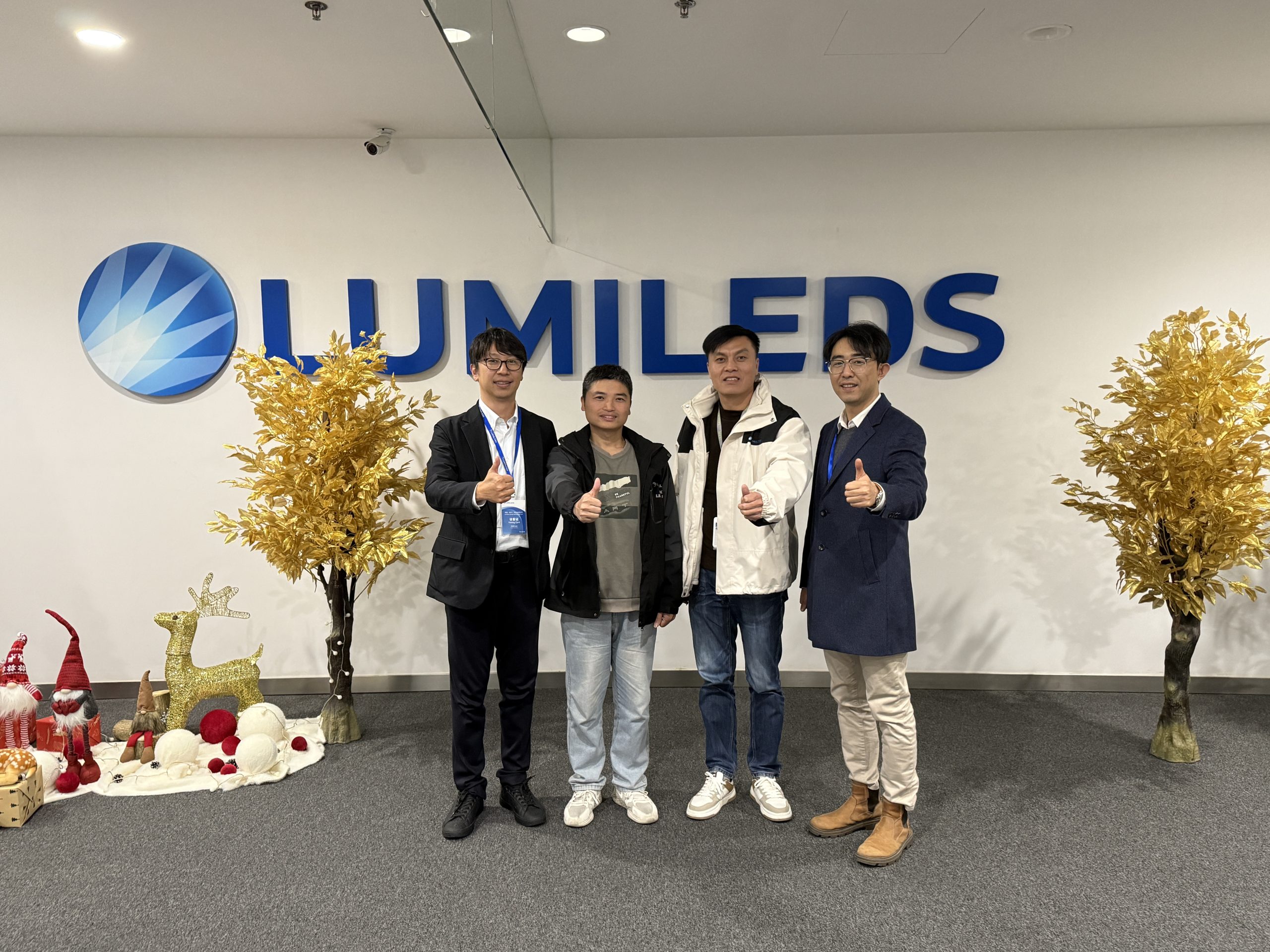
Taken inside the factory: From left, UNIX-Kono, Lumileds-Michael, Lumileds-Andy, UNIX-Lee
Why is Lumileds highly regarded in the industry?
Lumileds is a globally recognized company in the LED and automotive lighting sectors. Its products are widely used in various fields, including consumer electronics, automotive lighting, and medical devices. As a company that continues to grow based on technological strength, Lumileds sets extremely strict standards for product performance and quality.
However, as market demands shift and product designs become increasingly complex, Lumileds’ production line faced unprecedented challenges.
“Some of our LED modules have extremely small soldering points, making it difficult to ensure stable quality with conventional soldering methods. Additionally, as market demand increased, higher production efficiency was required. However, traditional manual soldering and early-stage automation equipment struggled to support mass production and complex operations,” explains the Lumileds engineering team.
Furthermore, some modules required soldering that combined different materials, necessitating highly adaptable equipment. In response to these challenges, Lumileds began exploring next-generation soldering solutions.
From Tradition to Smart Manufacturing: The Evolution of Lumileds
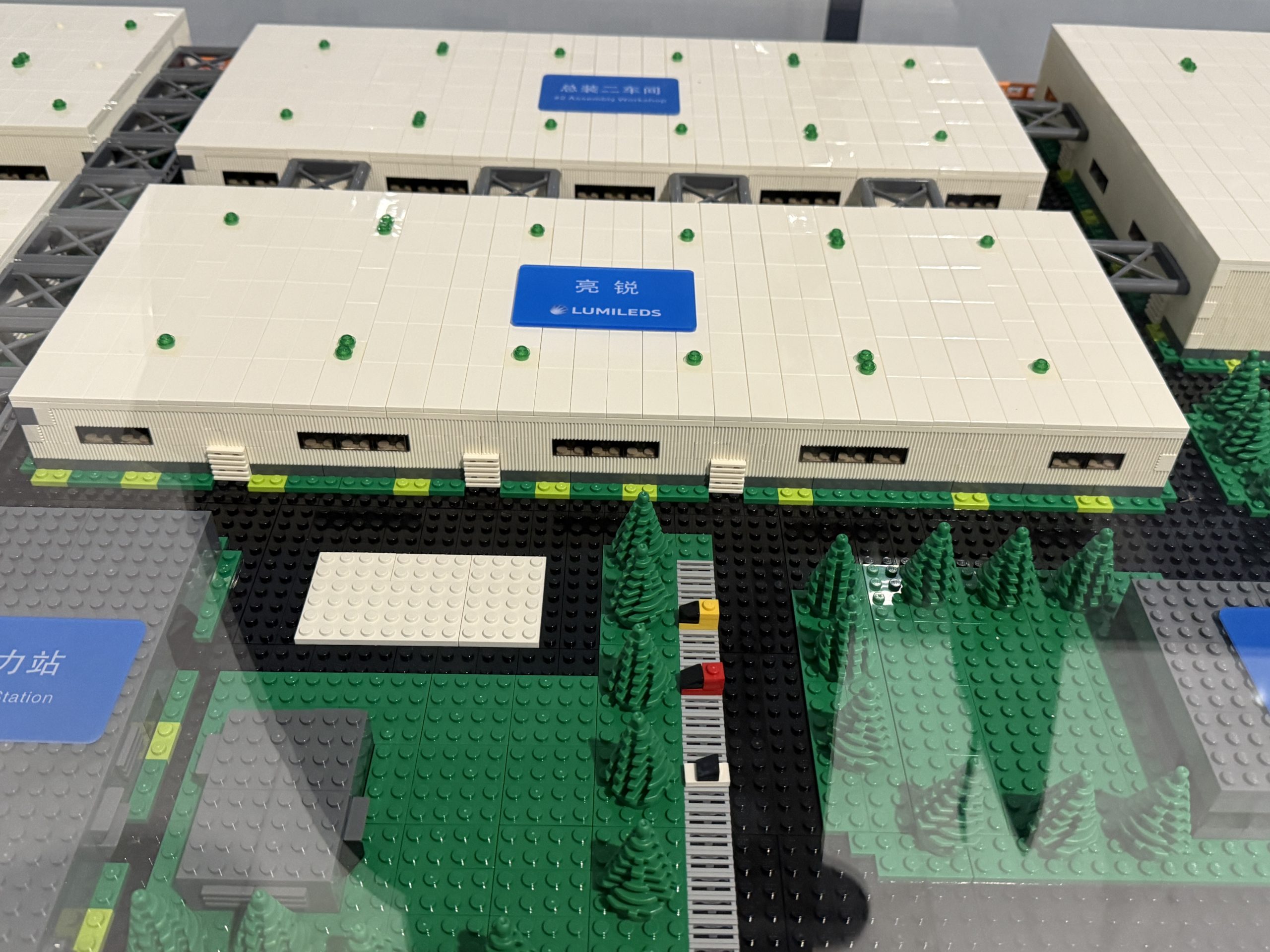
Reference product exhibited in the factory
How has Lumileds progressed in technological innovation?
Lumileds offers a wide range of products, from premium LED headlights to specialized lighting solutions, including the following representative series:
- LUXEON Go Series: A product for mainstream LED headlights featuring a compact design and integrated thermal management.
- LUXEON NeoExact Series: A matrix-type headlight solution characterized by chip-level packaging and flexible light source placement.
- LUXEON C & CZ Series: High-quality colorful light sources for architecture, entertainment, and emergency vehicles.
- LUXEON SunPlus: Optimized spectral support for greenhouse cultivation.
“We have led technological innovation from halogen lamps to xenon lamps and now LED lighting,” says Lumileds’ technical representative.
Additionally, the company is not only advancing lighting technology but is also actively involved in the development of smart and connected technologies in the automotive industry. This has driven further innovation in the market and created new growth opportunities.
Limitations of Traditional Soldering Technology: Emerging Challenges
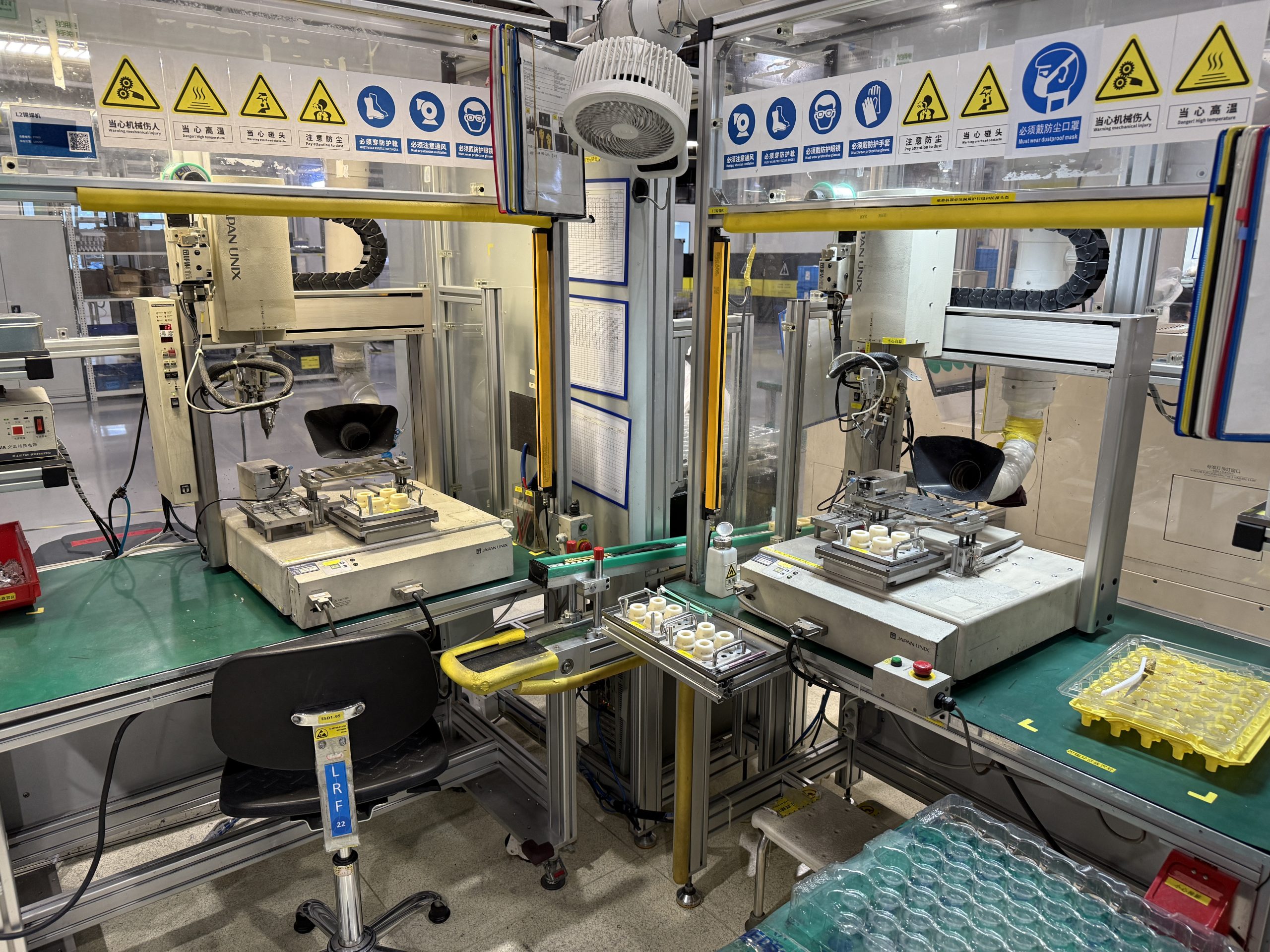
UNIX-41R/G introduced before laser soldering
What soldering challenges did Lumileds face at the time?
The engineering team at Lumileds had experimented with various soldering methods over the years. However, they found that traditional approaches could not fully meet manufacturing needs due to operator-dependent inconsistencies in manual soldering and the difficulty of wave soldering due to localized component shapes.
“Manual soldering heavily depends on the operator’s skill, leading to inconsistencies in product quality. Ensuring stable quality was particularly difficult for extremely small soldering points,” explains the production manager at Lumileds.
While automation equipment had been introduced for certain processes, it still could not handle more complex soldering requirements or high-precision demands.
“We upgraded existing automation equipment and optimized manual processes, but these were only temporary solutions. For critical components, the limitations of our equipment became a major obstacle,” he recalls.
Eliminating Production Bottlenecks Through Automation
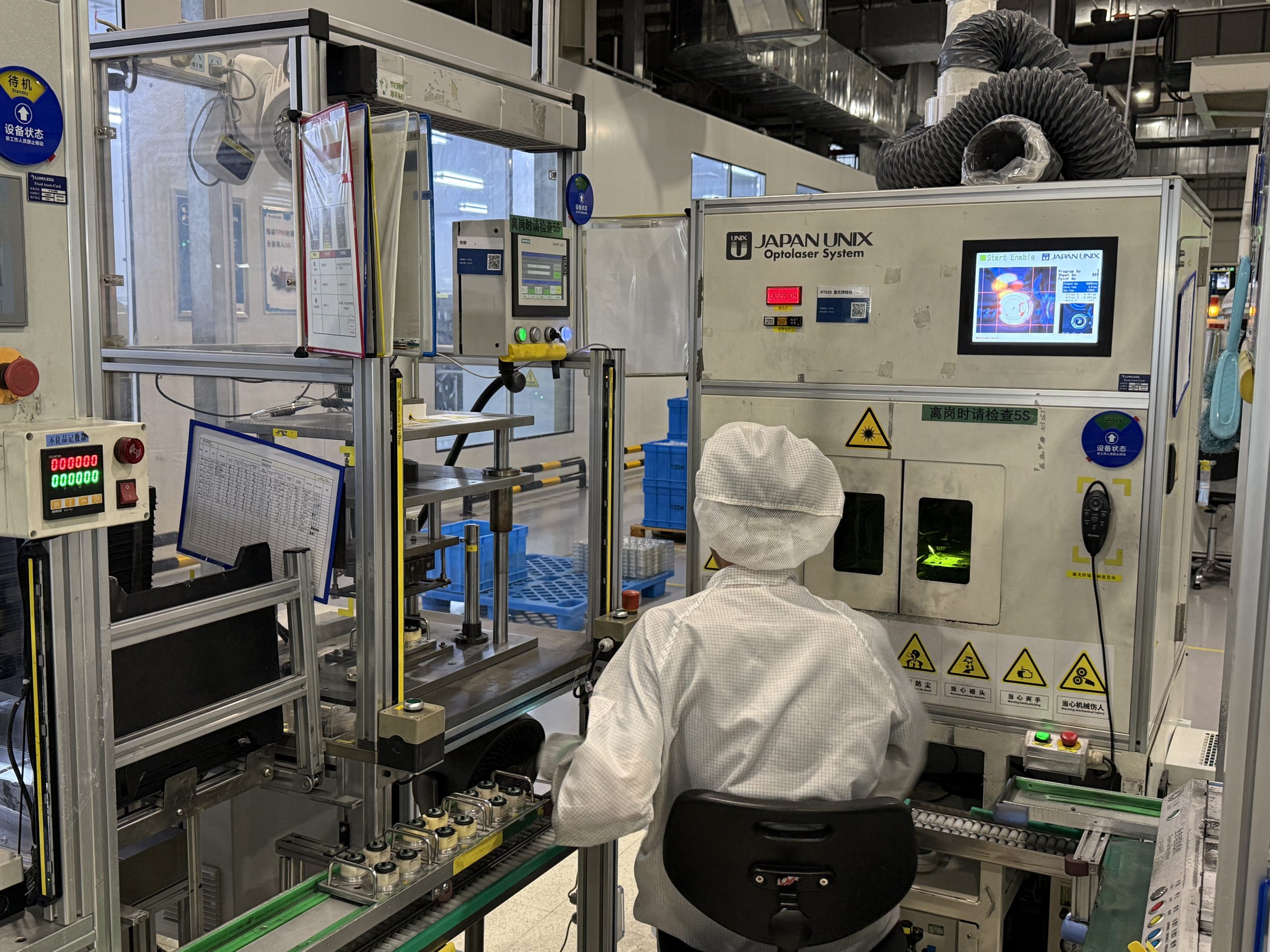
Laser soldering for cell production
How did Lumileds overcome its production challenges?
As part of its smart manufacturing strategy, Lumileds faced challenges related to improving production efficiency, reducing costs, and maintaining quality control. The automotive lighting industry requires extremely high precision, making it increasingly difficult for conventional manufacturing methods to meet market demands.
“To enhance headlight functionality and improve energy efficiency, we had to manage manufacturing costs, comply with regulations, and address technical complexities,” explains an engineer at Lumileds.
To tackle these challenges, Lumileds introduced Japan Unix’s automated laser soldering system in 2018. This equipment significantly improved production accuracy and consistency.
Additionally, by integrating a SCARA-type laser soldering robot, Lumileds dramatically increased production efficiency and strengthened its competitive edge in the global market.
From Needs Analysis to Solution Development
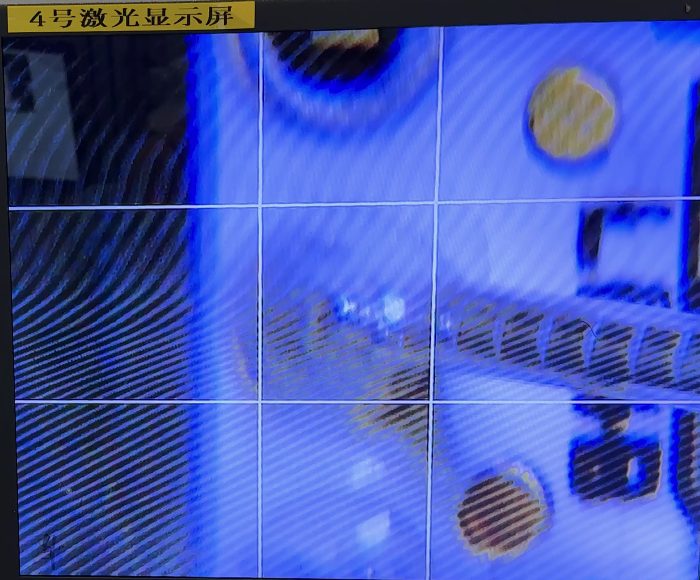
Actual laser soldering in progress
What specific requirements did Lumileds have for soldering equipment?
At the initial stage of the project, Japan Unix’s engineering team worked closely with Lumileds’ engineering team to conduct a thorough analysis of the production line. Through on-site inspections and data analysis, the key requirements for Lumileds’ soldering solution were identified as follows:
- High-precision soldering
- Improved production efficiency
- Adaptability to various materials
Extremely high positioning accuracy was required to accommodate small soldering points and complex layouts.
The equipment needed to handle high production volumes while maintaining consistent quality.
The ability to accommodate different material combinations and ensure long-term process stability was crucial.
To meet these requirements, a SCARA-type laser soldering robot was chosen as the optimal solution. This equipment featured a high-performance vision sensor for positioning, a real-time soldering management system, and flexible process configuration capabilities, making it a perfect fit for Lumileds’ production needs.
Implementation Process: From Trial Operation to Full Deployment
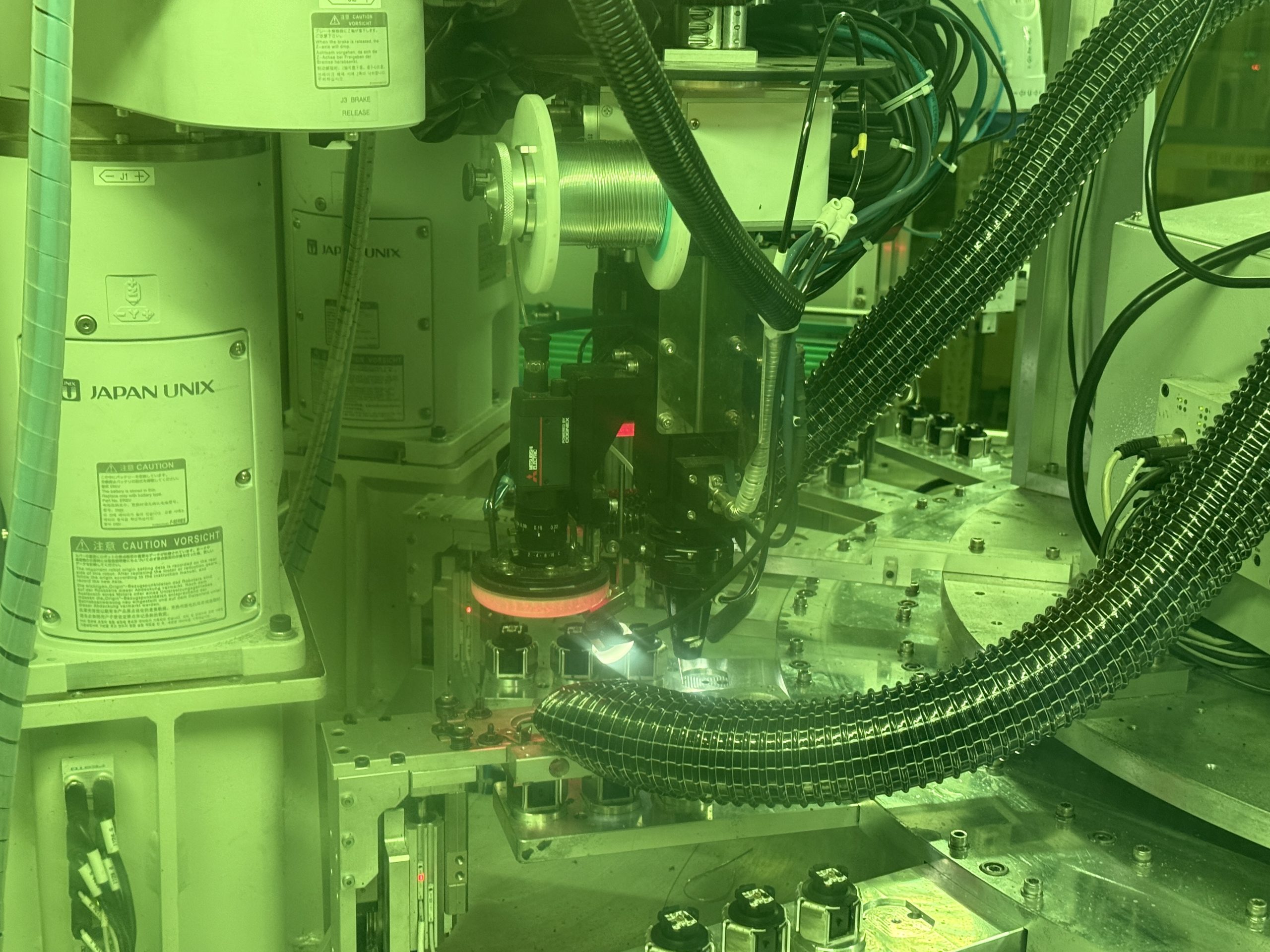
Center Red Light: Vision Sensor Function
How was the trial operation of the SCARA-type laser soldering robot conducted?
For equipment implementation, Japan Unix and Lumileds developed a meticulous testing plan. First, a specific production line was selected as a test environment to thoroughly evaluate the performance of the SCARA-type laser soldering robot.
During the trial phase, the robot’s high-precision vision sensor system demonstrated significant advantages.
- The vision sensor function quickly identified soldering points, performing operations with micron-level precision even in extremely fine areas.
- The soldering management system monitored parameters such as temperature, solder amount, and soldering time in real-time, ensuring optimal performance.
The success of this trial operation proved the reliability of the equipment, leading Lumileds to decide on full-scale implementation. Over the following months, additional SCARA-type laser soldering robots were gradually introduced, eventually operating across all major production lines.
Notable Achievements: A Dramatic Increase in Productivity
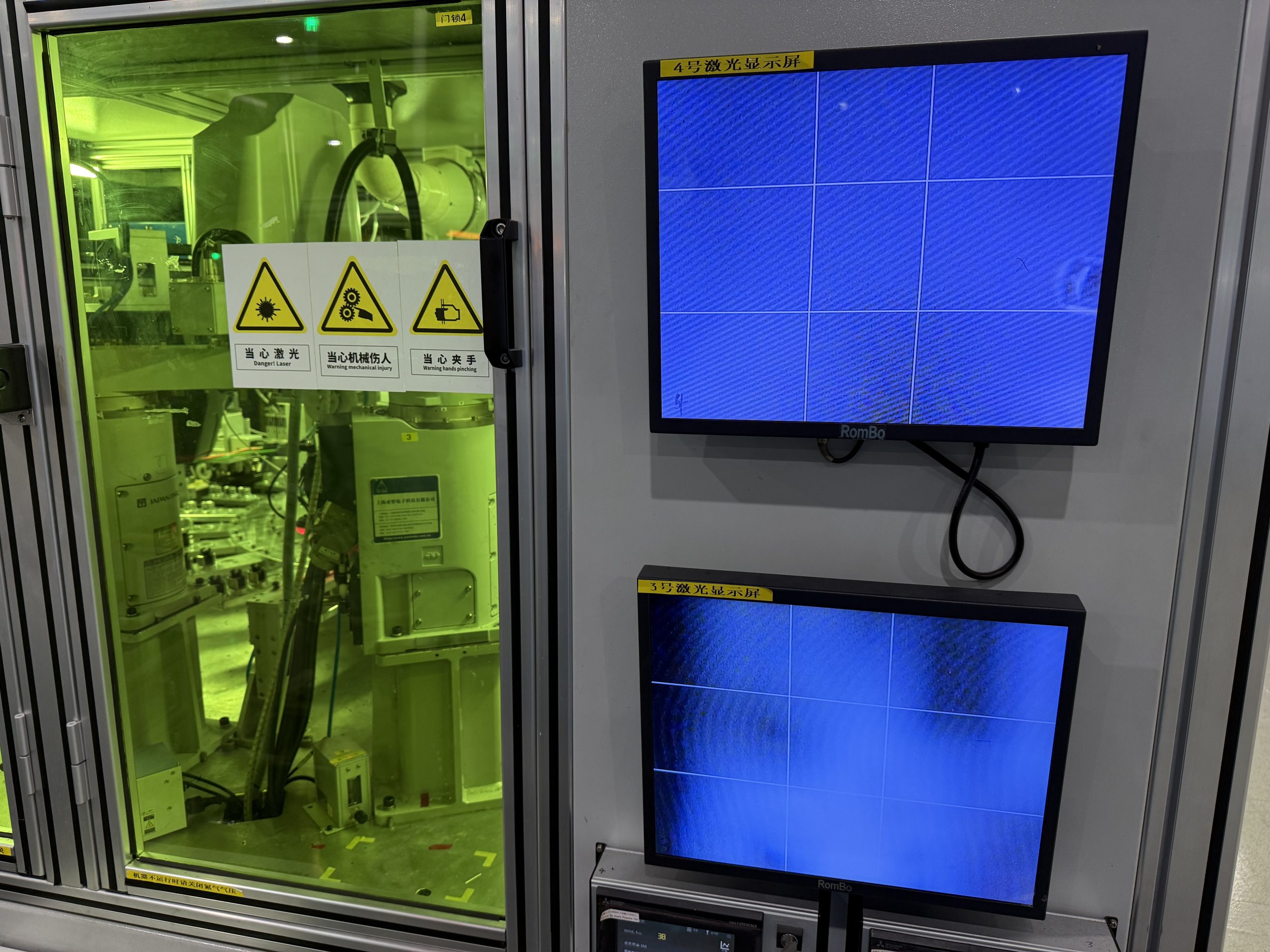
Real-time soldering data recorded by equipment
What specific results did Japan Unix’s soldering system bring?
The introduction of Japan Unix’s laser soldering system brought the following significant improvements to Lumileds’ production environment:
- Improved soldering precision
- Enhanced production efficiency
- Increased adaptability to various materials
The vision sensor system and highly rigid, high-precision robot increased soldering point accuracy by 30%, reducing defect rates and enhancing product reliability.
High-speed processing capabilities shortened production cycles by 40%, allowing for quick adaptation to market changes.
The system’s flexibility enabled handling of different material combinations, facilitating more advanced product designs.
“Japan Unix’s equipment not only solved our current production challenges but also opened new possibilities for future product development. We are highly satisfied with this partnership,” said Lumileds’ technical director.
Japan Unix’s Laser Soldering: A Solution Combining Precision and Efficiency
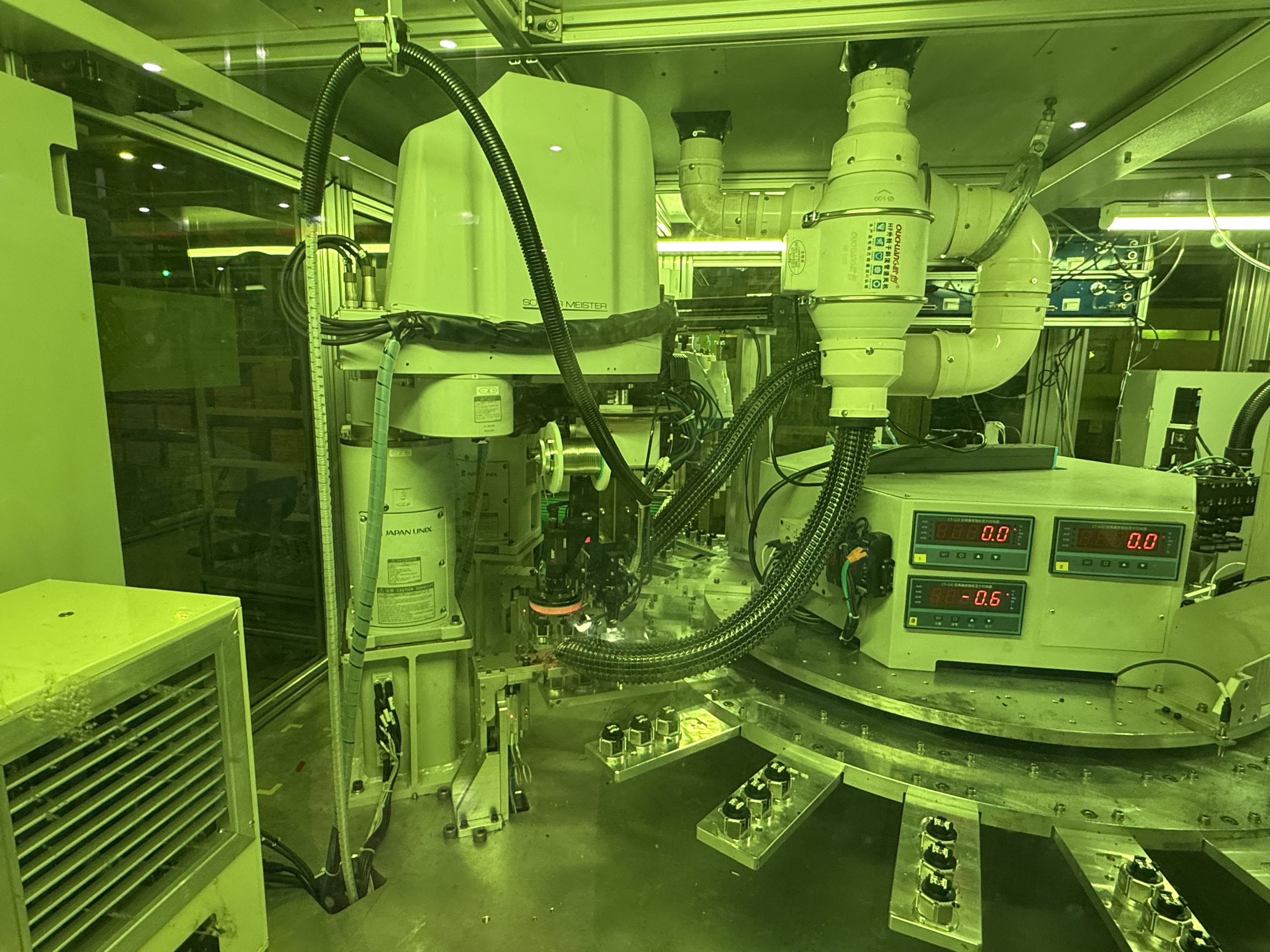
SCARA-Type Laser Soldering Robot
What were the key factors in Lumileds’ selection of Japan Unix’s laser soldering system?
When choosing Japan Unix’s laser soldering system, Lumileds prioritized the following aspects:
- High-precision soldering technology
- Wide adaptability of laser soldering
- Enhanced market competitiveness
Micron-level vision sensor functionality ensured stable quality control.
Capable of handling various materials and complex soldering requirements.
The introduction of a unique management system and specialized soldering robot technology secured a technological advantage in the global market.
“Japan Unix’s equipment is not just a production tool; it has become a key element in strengthening our competitiveness,” said the Lumileds engineering team.
Future Prospects: The Smart Factory Revolution Led by Laser Soldering
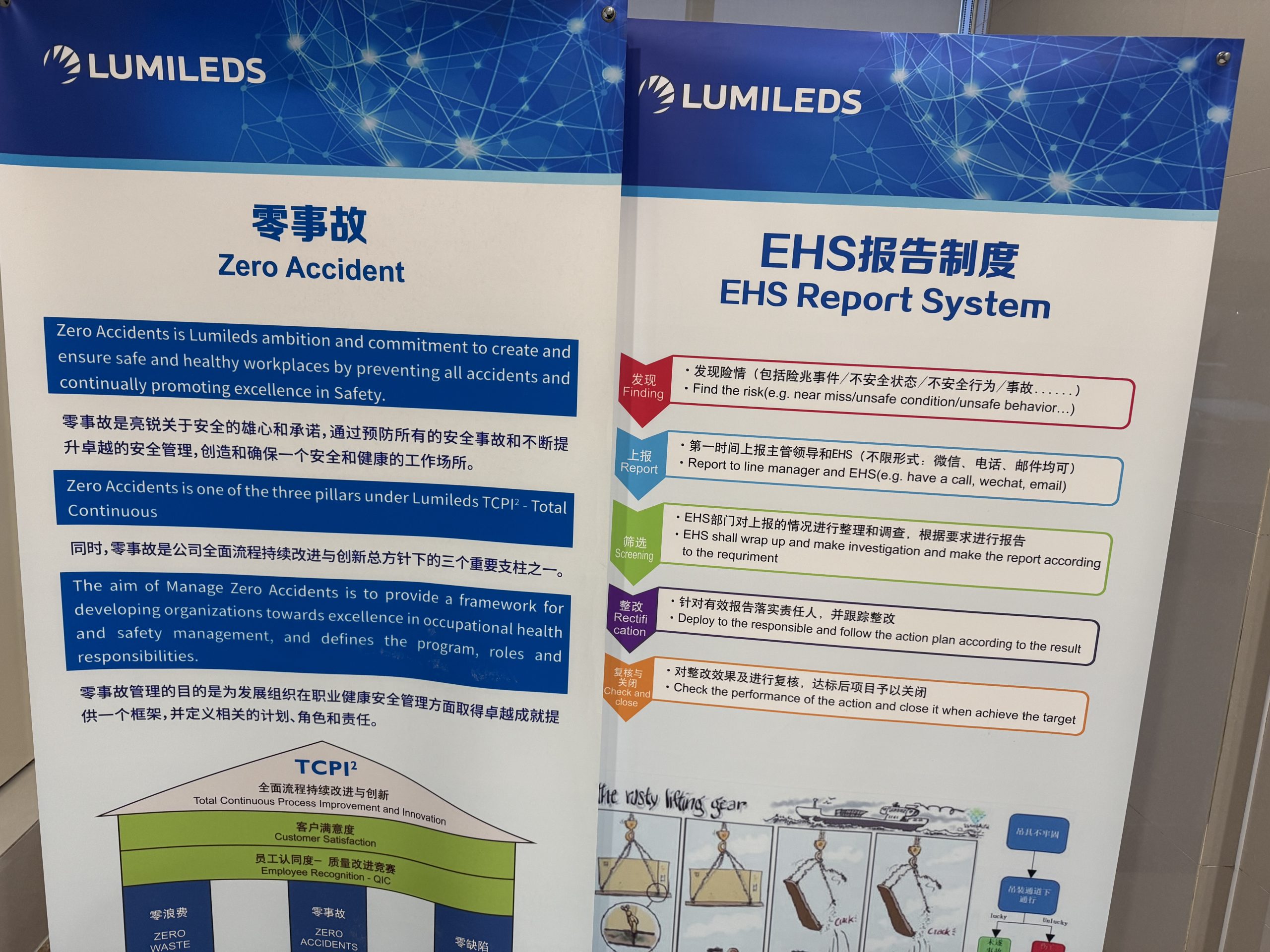
Lumileds’ Commitment to EHS (Environment, Health, and Safety)
What role does Lumileds expect laser soldering robots to play?
Moving forward, Lumileds aims to leverage laser soldering robots to achieve the following goals:
- Enhancing Production Efficiency and Sustainable Manufacturing
- Expansion into New Markets
- Integration with AI and IoT
- Improving Safety and Human-Robot Collaboration
Utilizing more efficient and environmentally friendly technologies to achieve sustainable production.
Expanding applications in high-value sectors such as renewable energy and precision equipment manufacturing.
Further advancing automation technology to develop more sophisticated smart production lines.
Establishing a safe working environment where humans and robots coexist, enhancing both operational efficiency and safety.
Through these initiatives, Lumileds aims to lead next-generation manufacturing and drive further industry development.
The introduction of Japan Unix’s laser soldering system has delivered the following achievements at Lumileds’ production sites:
- Improved Soldering Precision
- Increased Production Efficiency
- Greater Material Adaptability
The vision sensor system and high-precision, rigid robot improved soldering accuracy by 30%, reducing defect rates and enhancing product reliability.
High-speed processing capabilities shortened production cycles by 40%, enabling rapid adaptation to market changes.
The system’s flexibility allows for handling different material combinations, enabling more advanced product designs.
“Japan Unix’s equipment has not only solved our current production challenges but has also opened new possibilities for future product development. We are highly satisfied with this partnership,” said Lumileds’ technical director.
Industry Insights: Future Opportunities Brought by Automation
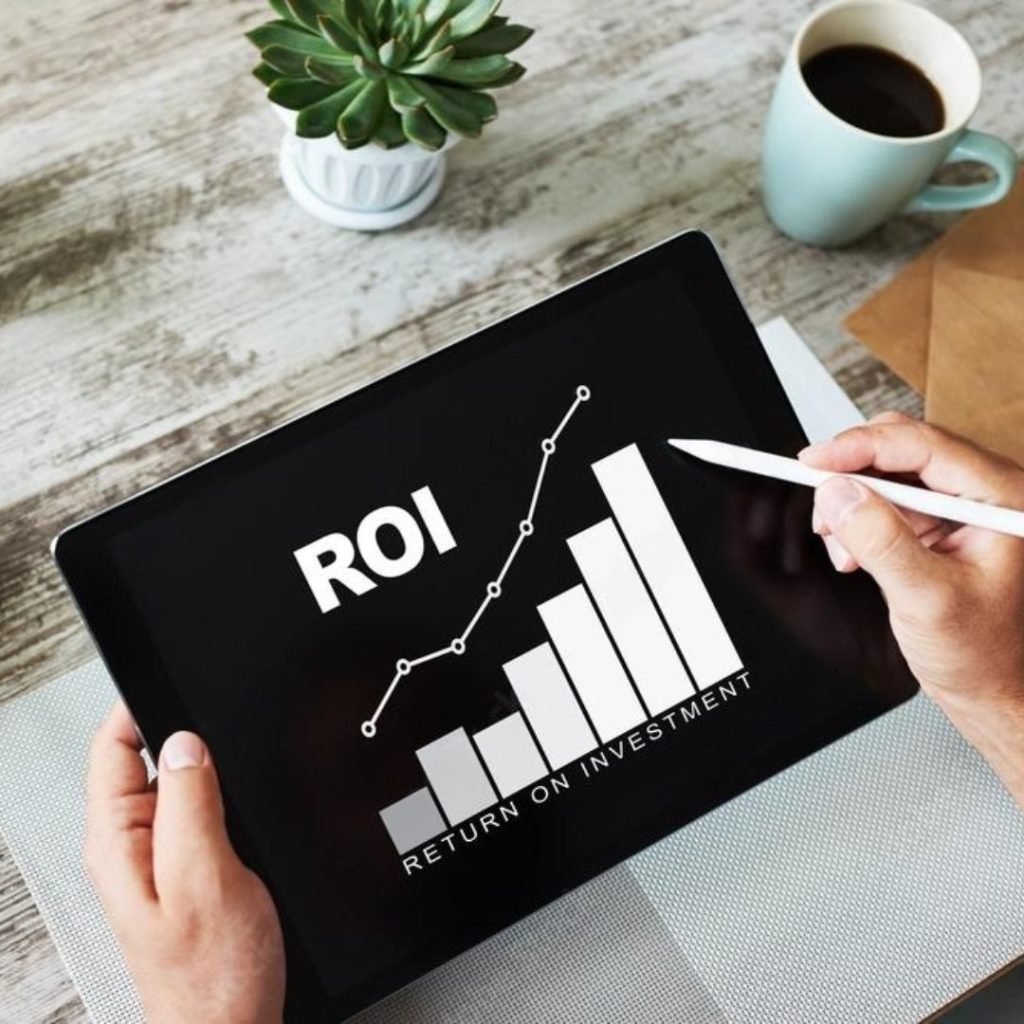
What are the key points for “successful automation” according to Lumileds?
When selecting Japan Unix’s laser soldering system, Lumileds prioritized the following aspects.
Having successfully implemented automation, Lumileds offers the following advice to other companies in the automotive industry:
- Establish Clear Standards
- Invest Aggressively in New Technologies
- Continuous Improvement and Education
Setting manufacturing standards is crucial to ensuring consistency and quality in the automation process.
Utilizing the latest technology leads to improved productivity and reduced risks.
Enhancing operator skills and optimizing processes enable stable, long-term automation.
Successfully transitioning from traditional manufacturing to smart factories requires not only technical expertise but also operational know-how. By leveraging cutting-edge laser soldering technology, Lumileds continues to enhance productivity and build a foundation for the future of manufacturing.
Japan Unix is committed to staying close to customer needs and providing cutting-edge soldering technology. The partnership with Lumileds represents not just a technical success but a significant step toward industry advancement.
If your company is facing soldering challenges in its manufacturing process, please contact Japan Unix. We will propose the optimal solution to support your company’s growth.