Case Study Interview: Production Engineer with 40 Years of Experience – Part 1
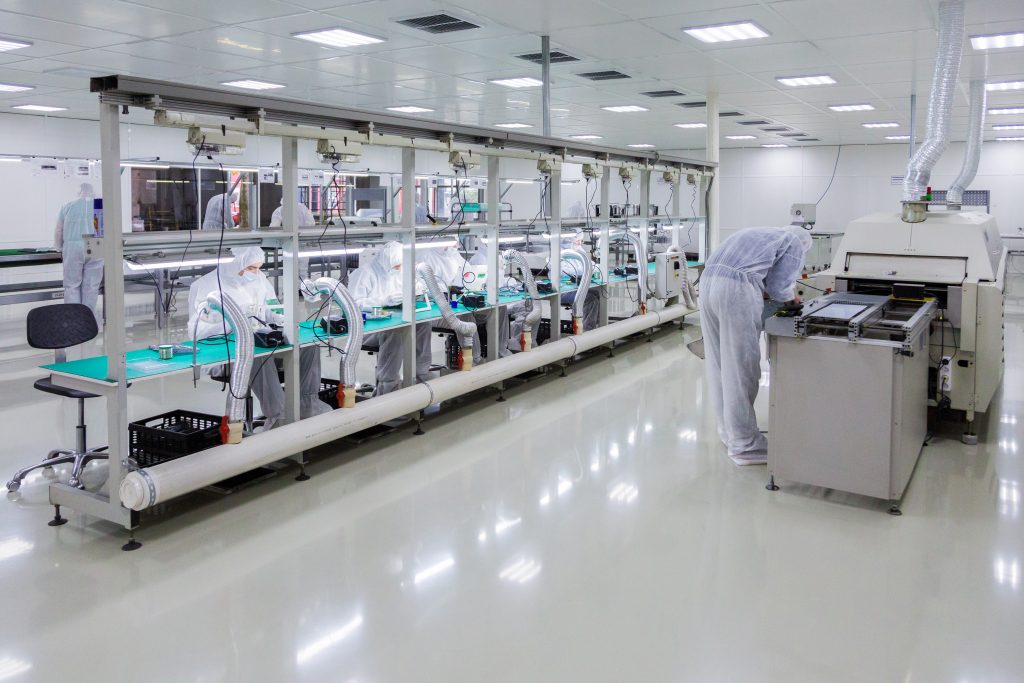
Case Study Interview
Production Engineer with 40 Years of Experience Part 1
Table of Contents
- History of Automation and Robotization in Soldering Processes
- 40 Years Ago, “Soldering is Done by Hand” Was the Norm
- Challenges with Quality Variations Due to Human Factors
- Developed Automatic Machines but Struggled with High Defect Rates
- First Intstallation of Japan Unix’s Soldering Robot in 1988
- Expanded Robot Implementation in the 1990s to Match Mass Production
- Reference Video
History of Automation and Robotization in Soldering Processes
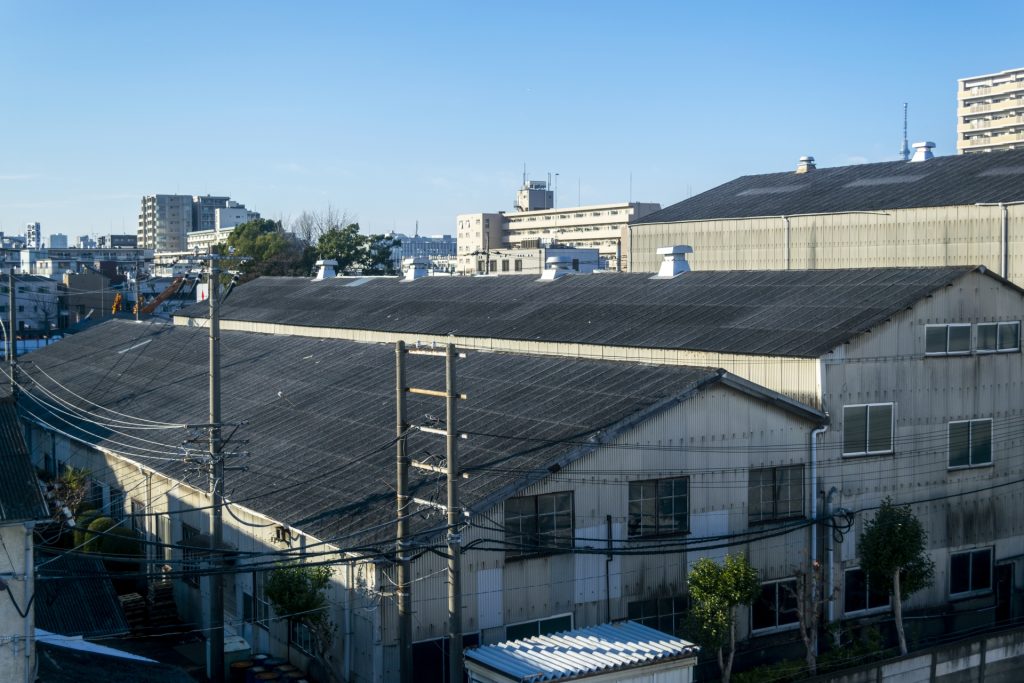
Today, soldering processes have advanced technologically and become automated, but reaching this point has been a long journey. We spoke with Mr. A, who has spent 40 years as a production engineer at a domestic electronics manufacturer, working on automating electronic component mounting processes. He reflected on the evolution of soldering processes and offered advice to the next generation of production engineers.
40 Years Ago, “Soldering is Done by Hand” Was the Norm
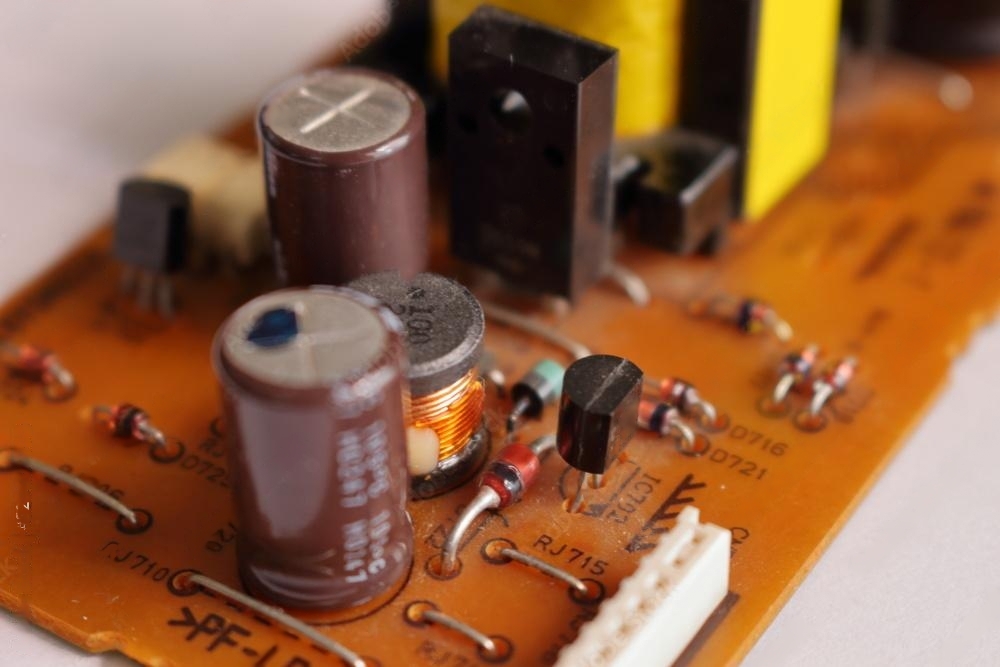
Board with Only Inserted Components
What was the soldering process like 40 years ago?
In the late 1970s to early 1980s, electronic devices used discrete electronic components with leads, rather than today’s chip components, soldered onto printed circuit boards. At that time, it was common for workers to solder manually, and we also believed that “soldering is done by hand.” The idea of automating soldering with machines, let alone robots, was almost nonexistent. There were many factory workers, and electronic components were relatively large, so with proper training, anyone could solder. We didn’t face issues like labor shortages as we do now.
However, since it was manual work, there were inevitable quality variations due to the skill level of the workers, such as too much or too little solder, which we recognized as a problem.
Challenges with Quality Variations Due to Human Factors
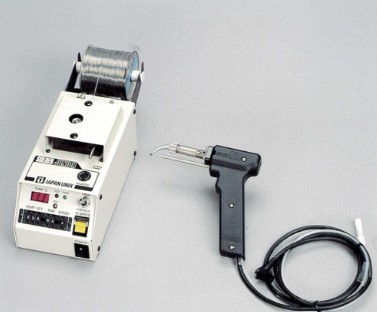
Soldering Iron with Automatic Solder Feeding Device (by UNIX)
Quality variations are an inevitable challenge in manual work.
At that time, the internal standards for appropriate solder amounts were ambiguous. Experienced technicians would visually assess and judge quality based on personal intuition, deeming it too much or too little. However, relying on an individual’s perception for quality standards isn’t proper management. We developed a quantitative solder supply device and introduced it to the production floor, standardizing the amount of solder fed to the iron. This resolved the quality variations caused by inconsistent solder amounts.
Developed Automatic Machines but Struggled with High Defect Rates
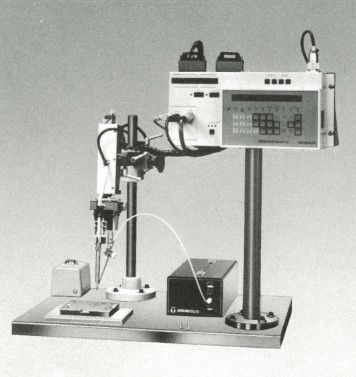
Simple Automatic Soldering Machine (Manufactured by UNIX)
Were soldering robots available at that time?
Japan Unix, as a soldering equipment manufacturer, was the first in the market to start selling soldering robots. However, at that time, many companies, including ours, still recognized soldering as a manual task.
By the mid-1980s, advancements in electronics technology led to the miniaturization and enhancement of electronic devices, introducing chip components. Surface Mount Technology (SMT) emerged as a new method for mounting components onto circuit boards, significantly changing mounting techniques.
Our product designs also transitioned to high-density mounting with narrow pitch configurations, and production quantities increased by an order of magnitude, requiring a new approach to manufacturing.
To address this, we developed our own automatic machine that used an air cylinder to move the soldering iron up and down. It was integrated with a workpiece feeding device and a solder feeding system to supply solder and press the soldering iron onto the workpiece for soldering.
The results, however, were disappointing. When performed manually, the defect rate was 1 in 50 units, or 2%. In contrast, our in-house automatic machine had a defect rate of 1 in 5 units, or about 20%. While it was able to mimic manual soldering to some extent and automate repetitive tasks, it was far from achieving satisfactory results. In terms of evaluation, it scored around 30 points—still a long way from passing.
First Installation of Japan Unix’s Soldering Robot in 1988
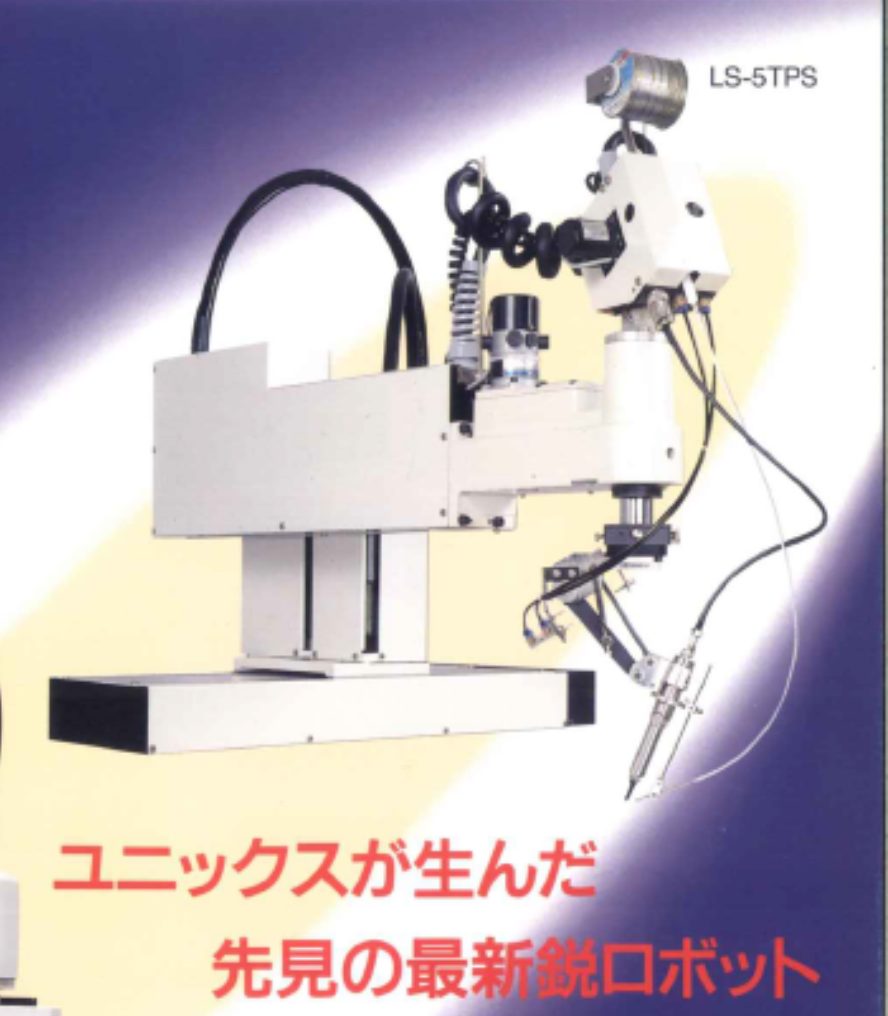
What did you do then?
As product designs shifted towards high-density mounting with narrow pitches and production volumes increased significantly, it became clear that our traditional methods were insufficient for manufacturing and quality assurance. The notion that “soldering is done by hand” had become a fixed idea. In this context, we encountered Japan Unix, which had already introduced soldering robots to the market, achieving automation in soldering processes.
We reached out to Japan Unix and installed our first soldering robot, a Cartesian-type model, in 1988. For chip components, we used SMT for mounting. For other discrete components, we placed them on the PCB and secured them with a jig to prevent them from falling when the board was flipped. After turning the board over, we used a soldering iron to solder the lead pins.
At that time, the soldering robot played a crucial role. Its numerical control capabilities and the ability to fine-tune accuracy through teaching were groundbreaking. This innovation made us realize that a new era of soldering had arrived.
Expanded Robot Implementation in the 1990s to Match Mass Production
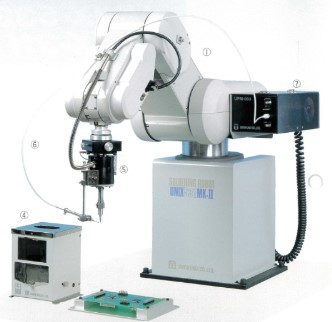
Vertical Articulated Robot UNIX-531MARKII
Did you then move towards full-scale robot implementation?
Yes, we did.
In the 1990s, driven by the wave of rationalization, we initiated a project to automate soldering tasks previously handled by 25 workers. We set a goal for soldering to achieve “three times the speed and ten times the quality” and decided to develop elemental technologies. In 1995, we invested approximately 200 million yen to establish a fully automated assembly line, incorporating six vertical articulated robots equipped with Japan Unix’s soldering units. Each robot performed continuous soldering on 21 points, completing each point in one second, and maintained a stable production with a yield rate exceeding 99.9%.
Securing internal approval for such a significant investment was challenging. By presenting concrete figures demonstrating the return on investment (ROI) and recovery plan, we obtained the necessary approvals. As a result, we recouped the investment in about three years, and the line continued to operate for an additional nine years, generating substantial profits post-recovery.
Related Products and Services
Click here for information on automatic soldering robots
Reference Video
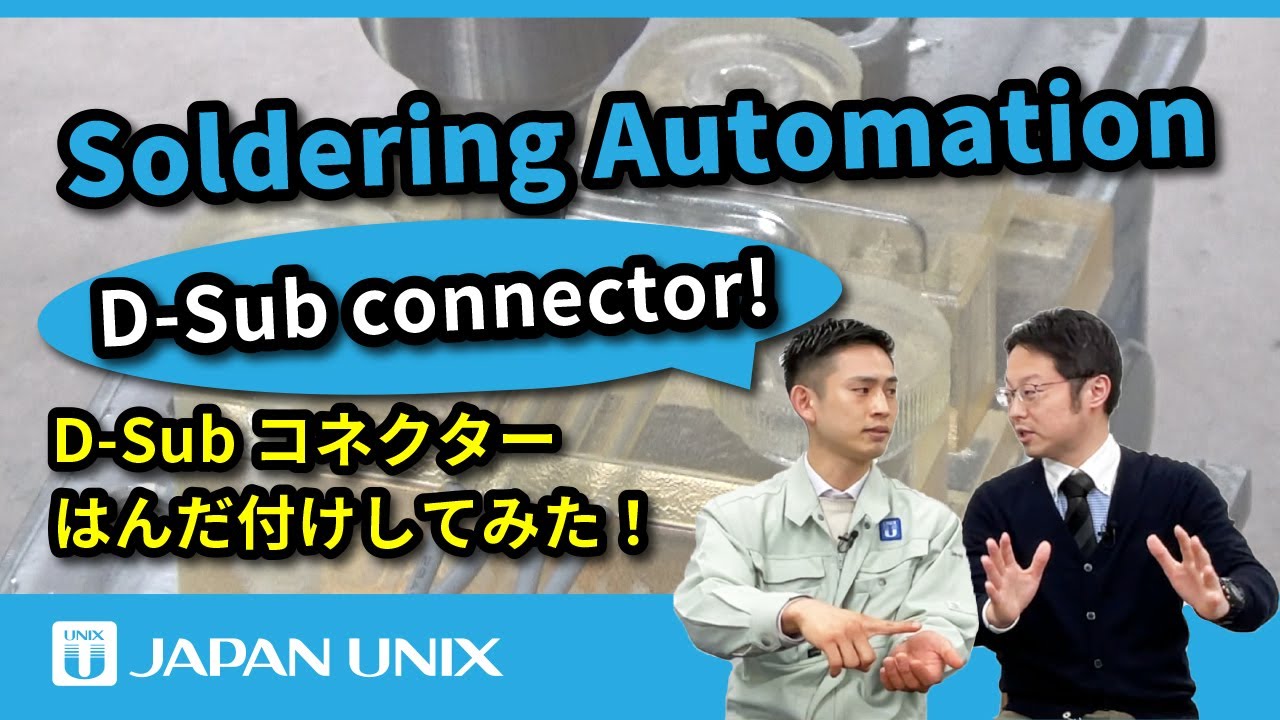