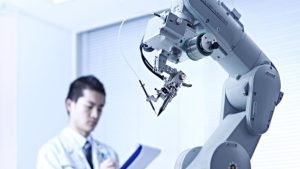
[2025年最新版]はんだ付けロボットとは?自動化のメリットや今後の課題について
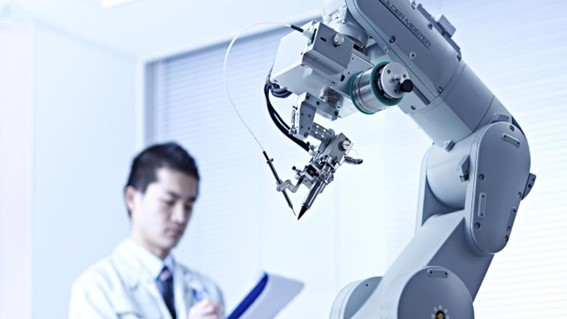
[2025年最新版]はんだ付けロボットとは?自動化のメリットや今後の課題について
はんだ付け作業を自動で行うはんだ付けロボット
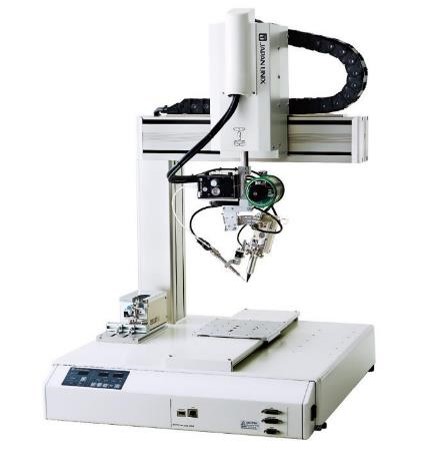
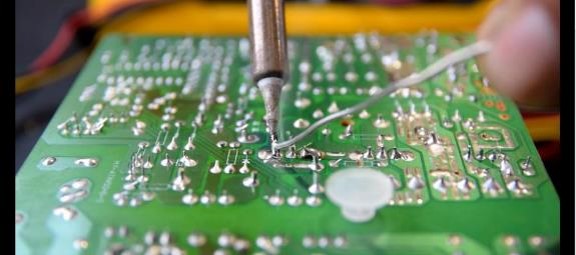
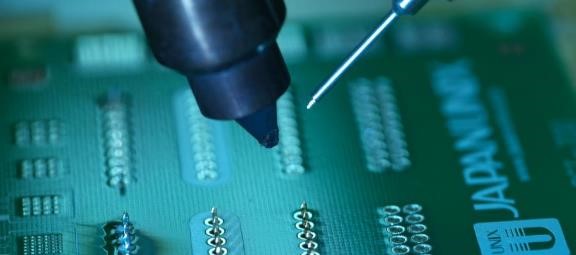
はんだ付けロボットとは、産業用ロボットの一種で、主にはんだ付け作業を行うロボットのことです。自動組立機に属し、人に代わって自動ではんだ付け作業を行います。
はんだ付けロボットが初めて登場したのは、自動車の組立や溶接、塗装ロボットなどが登場し、産業用ロボットというカテゴリーが確立された、1970年代以降のこと。ハンドの先端に「はんだごて」を持たせたものでしたが、当時はまだ精度も十分とはいえませんでした。はんだ付けロボット登場後も、はんだ付けは基本的に職人技であり、熟練工の仕事だったわけです。
しかし、技術の進歩とともに、はんだ付けロボットの技術精度は向上。加えて、2000年代からの鉛フリーはんだへの移行により、はんだ付けの難度が上がったことに加え、基板設計の複雑化や人手不足、技術継承の困難などを背景に、はんだ付けロボットは広く普及するようになりました。
人とロボットの大きな違いは、技術の習熟にかかる時間です。熟練のはんだ付け作業者は、感覚による微調整ができるため、微細な箇所のはんだ付けに向いています。ところが、その技術レベルに達するには、ある程度の年月をかけた訓練が必要です。
現在のロボットは、初期設定後すぐに稼働でき、導入したその日から、人より高速でのはんだ付けが可能です。
自動はんだ付け装置とはんだ付けロボットの違い
はんだ付けを自動化する方法は、効率良くまとめてはんだ付けを行う「自動はんだ付け装置」と、細かく精密にはんだ付けを行う「はんだ付けロボット」の大きく2つに分けられます。それぞれ得意・不得意な作業が異なるため、生産の現場ではラインに合わせて使い分けています。
自動はんだ付け装置
自動はんだ付け装置は、同じ物を大量生産したい場合に向いている方法です。あらかじめ溶かしたはんだを、はんだ付けする部分にあてて接合する「フロー方式」と、はんだ付けする部分にクリーム状のはんだを塗って部品を設置してから、熱ではんだを溶かして接合する「リフロー方式」の2つの方法があります。
どちらも、電子部品を効率良く、基板にまとめてはんだ付けしたい場合に使われます。ただし、フロー方式は小さい部品が密集した部分など、細かいはんだ付けには向いていませんし、リフロー方式は熱に弱い部品のはんだ付けなどには使用できません。
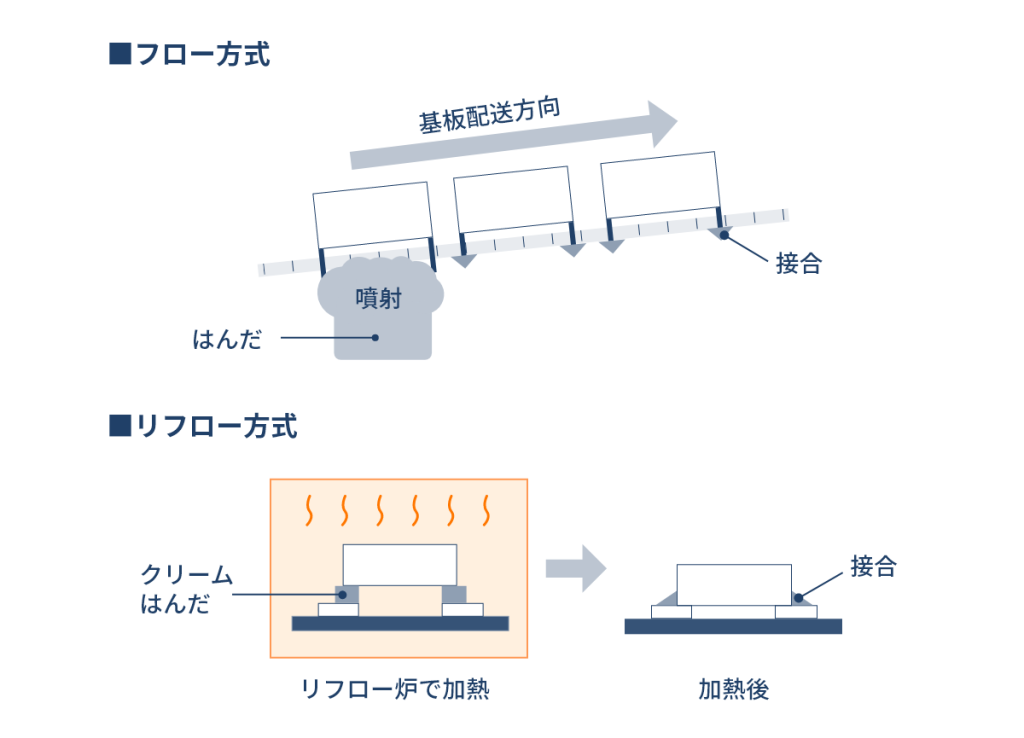
はんだ付けロボット
はんだ付けロボットは、自動はんだ付け装置ほど効率は良くありませんが、さまざまな品種の生産に向いています。局所的なはんだ付けや、熱に弱い部品のはんだ付け、細かく精密なはんだ付けが得意で、これらを正確に繰り返し行うことができるのが強みです。
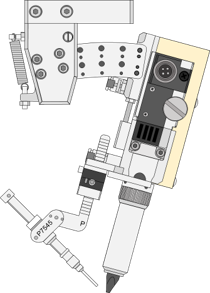
はんだ付けロボットのメリット
はんだ付けロボットが優れている点は、「繰り返し同じはんだ付け動作を行う再現性」「品質の安定(定量)化」「データの見える化」の3点です。
例えば、ジャパンユニックスの はんだ付けロボットの場合、こて先位置補正機構により、±0.05mmの補正精度ではんだ付けを行う位置を修正し、高い再現性を保証しています。さらに、はんだの送り量や速度、上昇・下降の各アプローチなど、最大255の項目について最適な条件を設定することで、品質の安定性を実現しています。
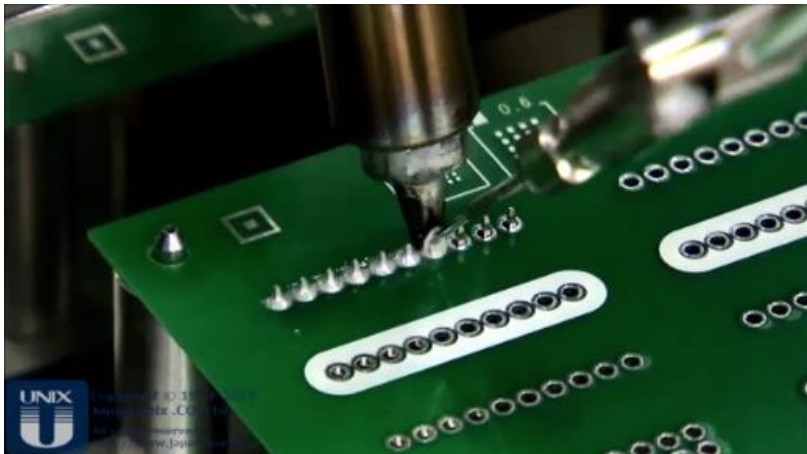
加えて、さまざまなログデータを保存できることで、生産過程のデータを残すトレーサビリティを確保。はんだ付け温度のモニタリング、カウンター設定、 エラー履歴の保存・閲覧、QRコード管理なども行うことができます。
こうして、同じ作業を人が行う場合と比べて、高速かつ高い正確性を持ってはんだ付けができるのが、はんだ付けロボットを導入するメリットです。
はんだ付けロボットのデメリット、苦手なこと
はんだ付けロボットは、最大のデメリットはメンテナンスを怠ると不良を発生させてしまうことです。コテ先の摩耗、軸やセンサーについたフラックスの清掃不足、こて先に残ったフラックスの炭化物、クリーナーはんだカスの清掃不足などが多くの不具合の原因となっており、初めてはんだ付けを取り扱う現場管理者や定期点検の現場指導者などの頭を悩ませます。今後は、メンテナンスを自動化するための、再現性のある機能や手法がより多く求められるでしょう。
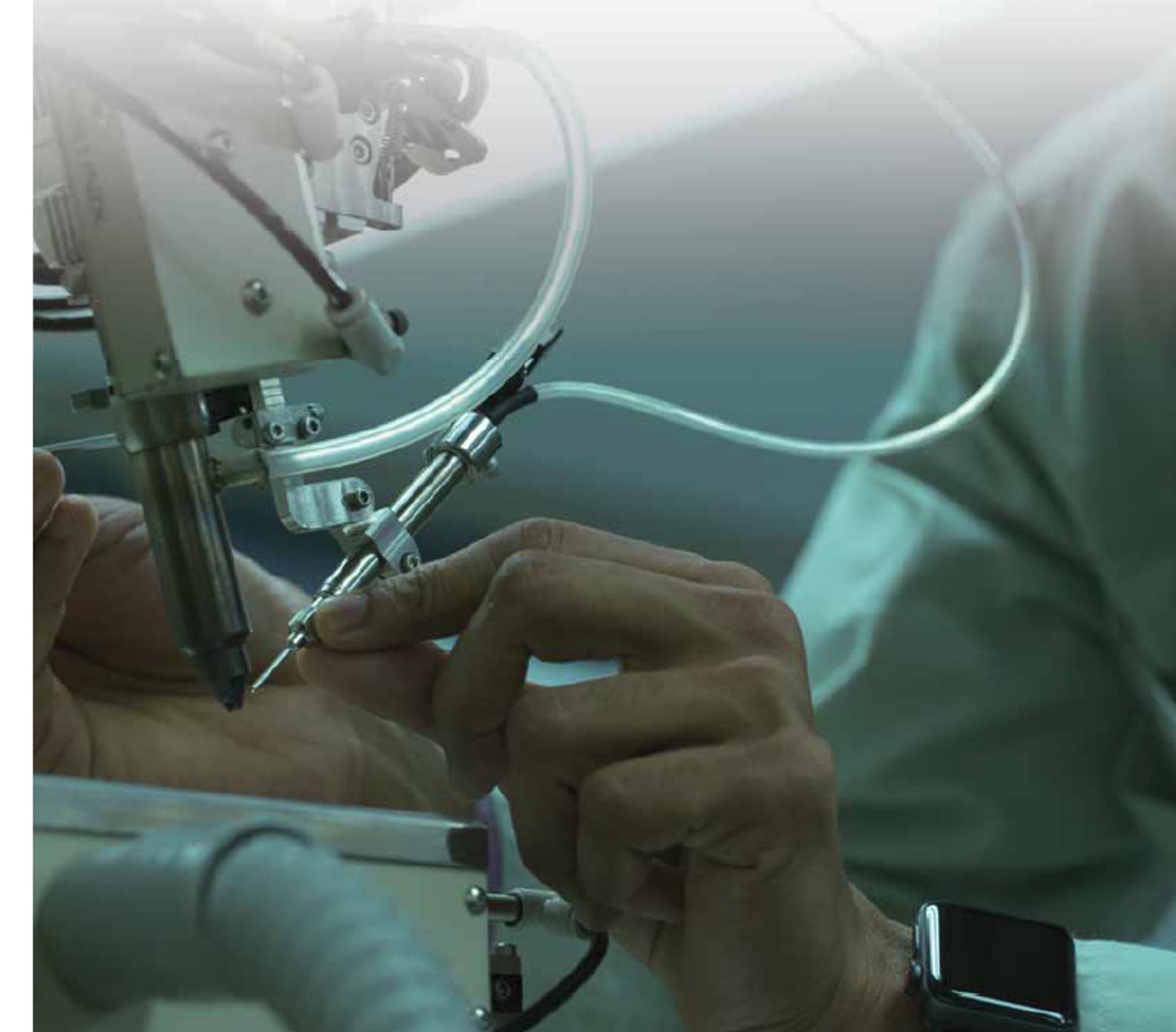
はんだ付けロボットの歴史
はんだ付けは、手の感覚、目の判断、嗅覚、音の変化、総合的な頭脳での判断が必要となる技術だけに、その自動化は、一般的な産業用ロボットの登場に比べて、少し時間が必要でした。
ジャパンユニックスが自動機メーカーと共同で、「人間の手の動き」を目指した最初のはんだ付けロボットを開発したのは、1980年代初頭のこと 。やがて1983年には、本格的なはんだ付けロボットの供給を開始します。
1985年には、垂直多関節5軸のはんだ付けロボット「UNIX‐511」が完成。以降も、性能向上のための研究開発を続け、繰り返し精度、動作速度、外部入出力など改良を加えながら、現在へと至ります。
なお、以前は「人が行う簡単な作業の代替え」だったはんだ付けロボットですが、はんだ付けの熟練工の減少もあり、現在は「人では難しいから、ロボットで対応したい」へと、ユーザーニーズに変化が表れています。
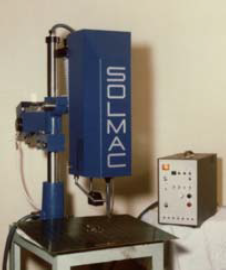
現在のはんだ付けロボット
現在のはんだ付けロボットは、その用途や加熱方式、構造によりさまざまな種類があり、ニーズに応じて最適な物を選べるようになっています。
用途
・ポイントはんだ付け
・引きはんだ付け
加熱方式
・こて加熱方式
(ヒーター式、誘導加熱式)
・レーザー加熱方式
・超音波加熱方式
構造
・垂直多関節型
・水平多関節型
・直交デスクトップ型
・直交型 など
はんだ付けロボットの構造による種類
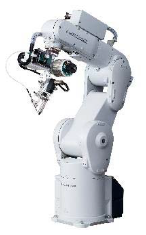
「垂直多関節型(5軸、6軸)」
立体的なワークも可能な万能型
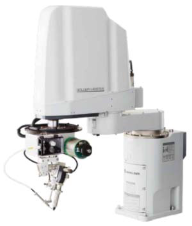
「水平多関節型(スカラ型)」
⾼速で平⾯精度が良い
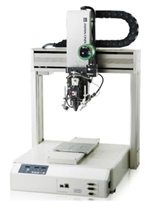
「直交デスクトップ型(4軸)」
ライン構成が不要で、導⼊しやすい
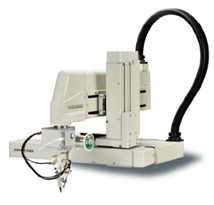
「直交型(4軸インライン型)」
平⾯精度が良く、平⾯基板に最適
これからのはんだ付けロボットに求められるもの
現在、製造業は人手不足や技術承継、IT活用の遅れのほか、カーボンニュートラルやSDGsに則った形態への転換など、さまざまな課題を抱えています。はんだ付けロボットには、こうした課題解決につながるものが求められています。今後のはんだ付けロボットを考えるとき、特に重要になると思われるのは、次の4つの視点です。
人手不足への対応
近年、はんだ付けロボットは人手不足になりし、コネクタ、ハーネスなどの「多品種少量」「固定が難しい製品」にも対応が必要となりました。精度の高い治具や製品形状に合わせたカスタマイズこて先、再現性を高める高精度な制御機能により、段取り替えが頻繁な場合でも柔軟な対応が可能になってきています。
また、「極端に狭いエリア」での作業も、センサ技術や、カメラ技術、微細動作の進歩により、安定した品質が確保されています。難しいとされていた領域にも対応できる場面が増えており、人手不足への効果的な対策として活用が進んでいます。
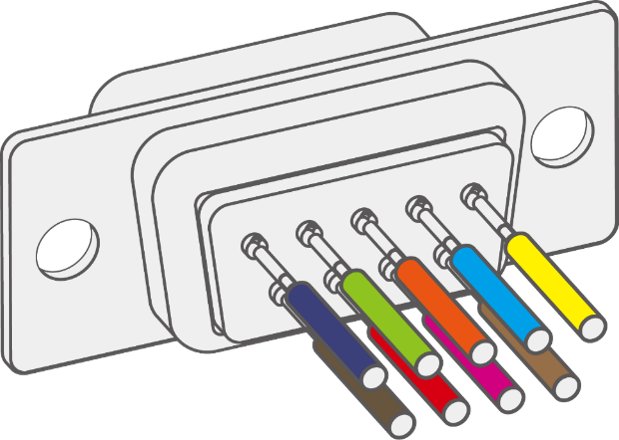
はんだ付けプロセスのさらなる見える化
生産効率の最適化・向上や、少ない人手での製造を可能にするには、さまざまなデータを収集して製造現場を「見える化」する、DX(デジタルトランスフォーメーション)化は欠かせません。DX化を考えたとき、はんだ付けロボットに必要なのは、熟練工の技をロボットが再現可能なはんだ付けプロセスに分解し、数値化できる機能です。
今後は、これまで熟練の現場管理者や保守管理者によって支えられてきた品質・生産スピードの改善や、トラブルの予防・予知を、誰でも実行できるようになる機能が求められるでしょう。
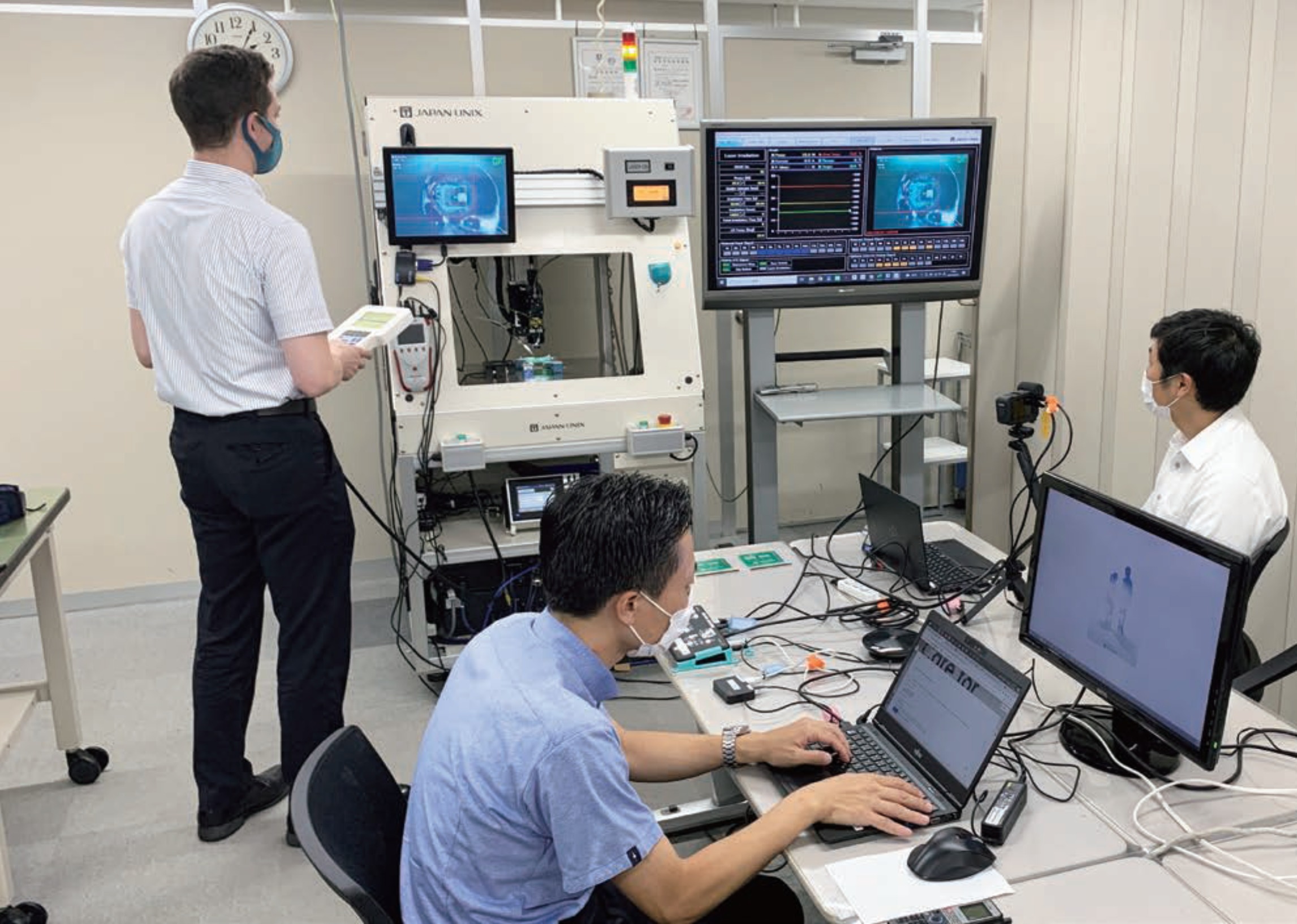
多品種少量・変種変量への対応
今後、世の中の製品は、よりお客様のニーズに合わせて個別最適化され、生産ラインも多品種少量化がさらに進んでいくと考えられます。そのため、はんだ付けロボットにおいても、ライン構成としてよりフレキシブルに対応ができるものが求められ、多品種対応・切り替えの簡易化、自動化などが必要となるでしょう。
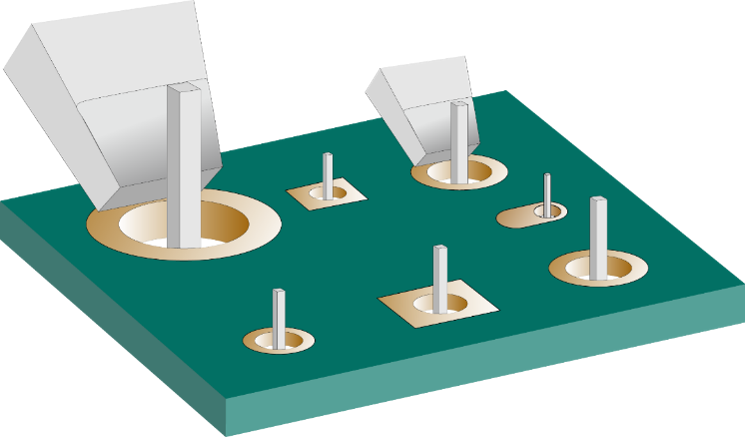
CO2削減目標へのアプローチ
今や、環境やSDGsへの配慮は、製造業全体の常識となっています。各国の政府や大手メーカーは、CO2削減目標の設定や、目標達成のための工場単位でのCO2削減アクションなどを始めています。
そういった時代の流れの中では、電源制御やモーター制御の製品などの高熱容量で高難易度のはんだ付けが増えていきます。
こうした動きの中、ポイントごとで条件を変えることができ、局所で必要な熱容量を加えることで、余計な電力を使わないはんだ付けロボットの需要は、さらに高まるでしょう。

医療機器、ヘルスケア、5G・6G高速通信領域でMEMS、超微細製品の増加
医療機器ヘルスケア、6G高速通信分野では、MEMSや超微細部品の需要が急増しています。この流れに伴い、接合精度と再現性が求められ、従来の方法では対応が難しくなっています。レーザーはんだ付けは低熱影響で高精度な接合を可能にし、先端の細いこて先と糸はんだの供給技術も、超微細な部品へ効率よく正確に材料を供給する点で重要視されています。これら先端技術は、命に関わる医療機器の安全性や高速通信機器の信頼性確保を支え、はんだ付けロボットのさらなる需要拡大を後押ししています。

はんだ付けロボットの進化は今後も続く
20世紀後半に誕生したはんだ付けロボットは、絶え間ない開発・改良により、格段の進化を遂げました。ですが、いまだ人間の作業者に代わって、すべてのはんだ付けをこなせるわけではありません。なぜなら、はんだ付けロボットには、人間が持つ目・鼻・耳・手からの感覚、そして頭脳が備わっていないためです。
センシング性能はめざましく向上していますが、熟練工の域に達するには、まだ道は長いといえるでしょう。今後も、ロボット本体の基本的改良やはんだ付け機能の向上、そしてソフトウエアの進化は、ますます進むと予想されます。
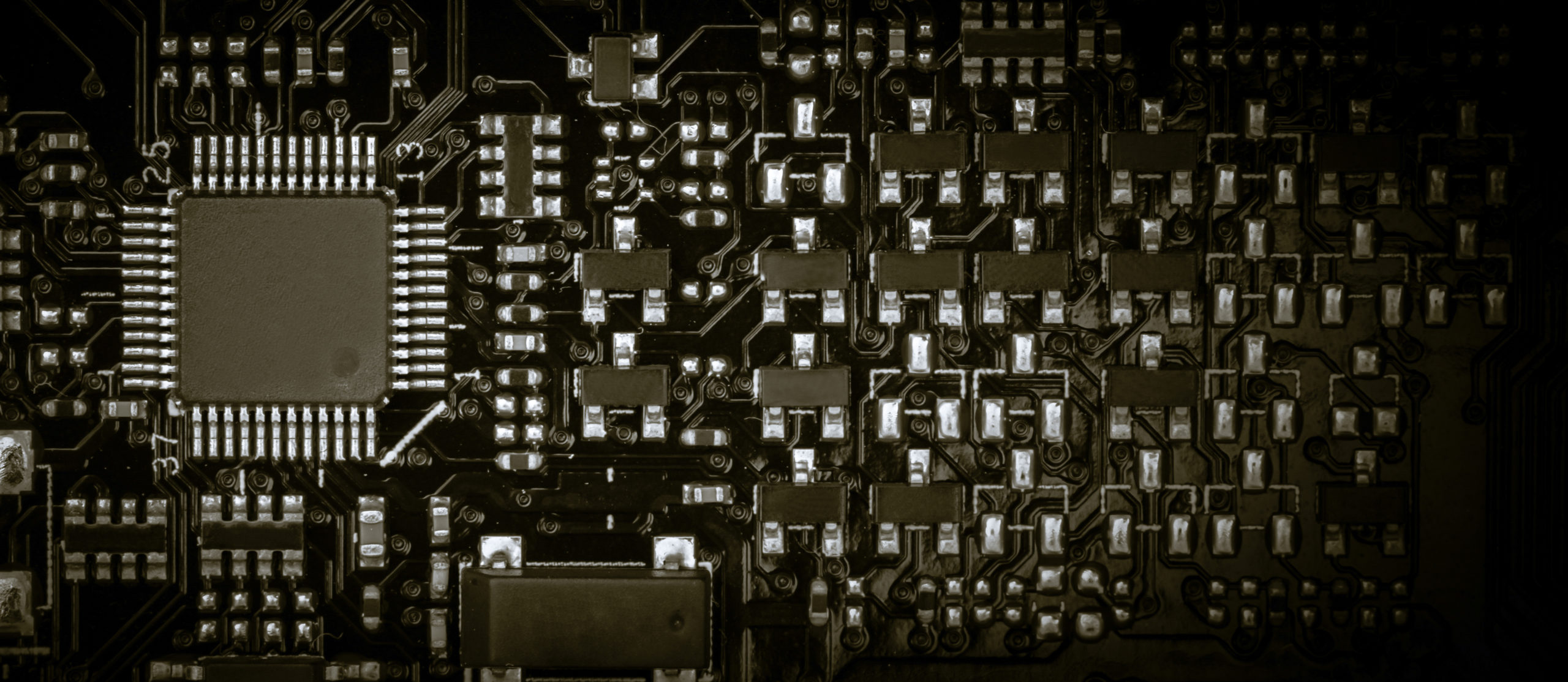
関連製品・サービス
関連動画
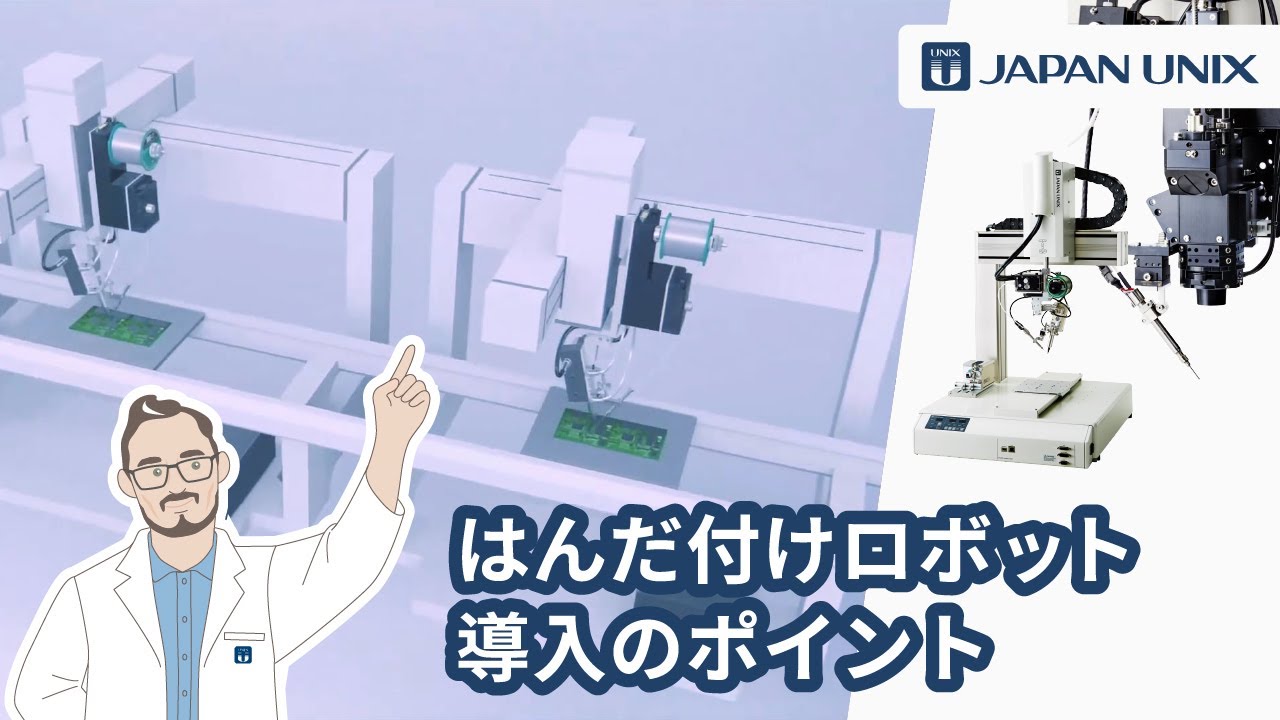
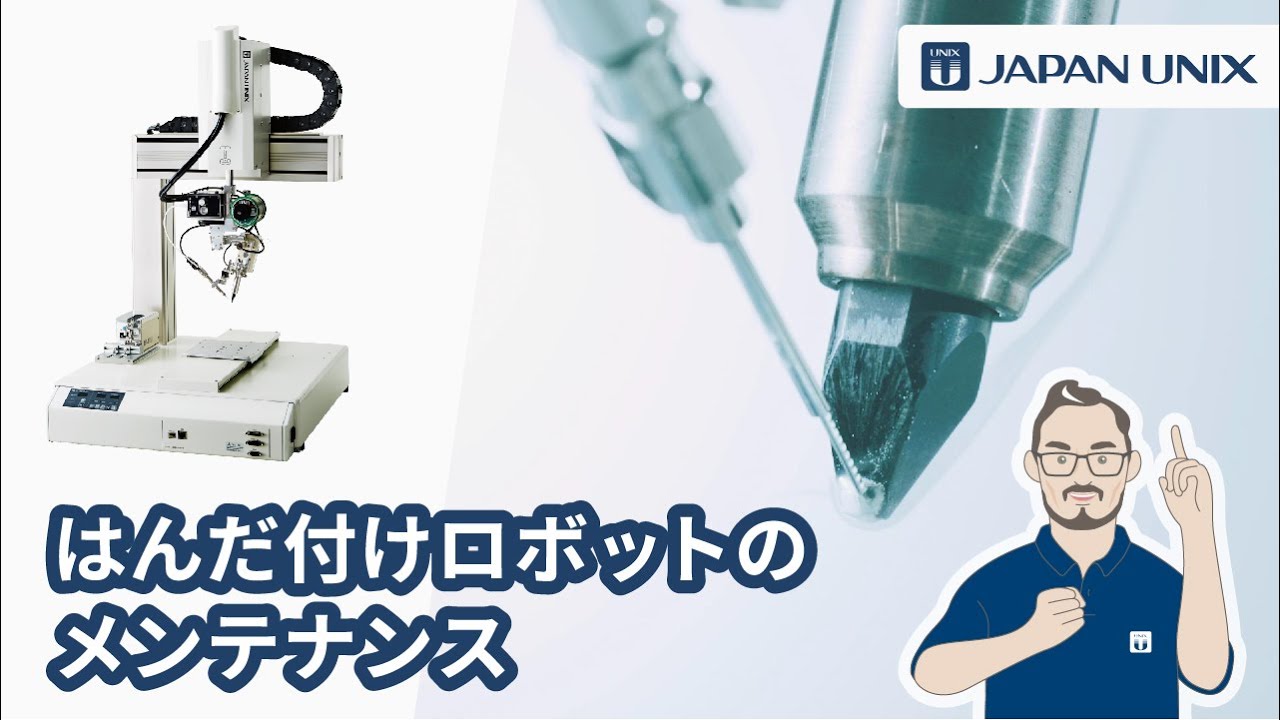
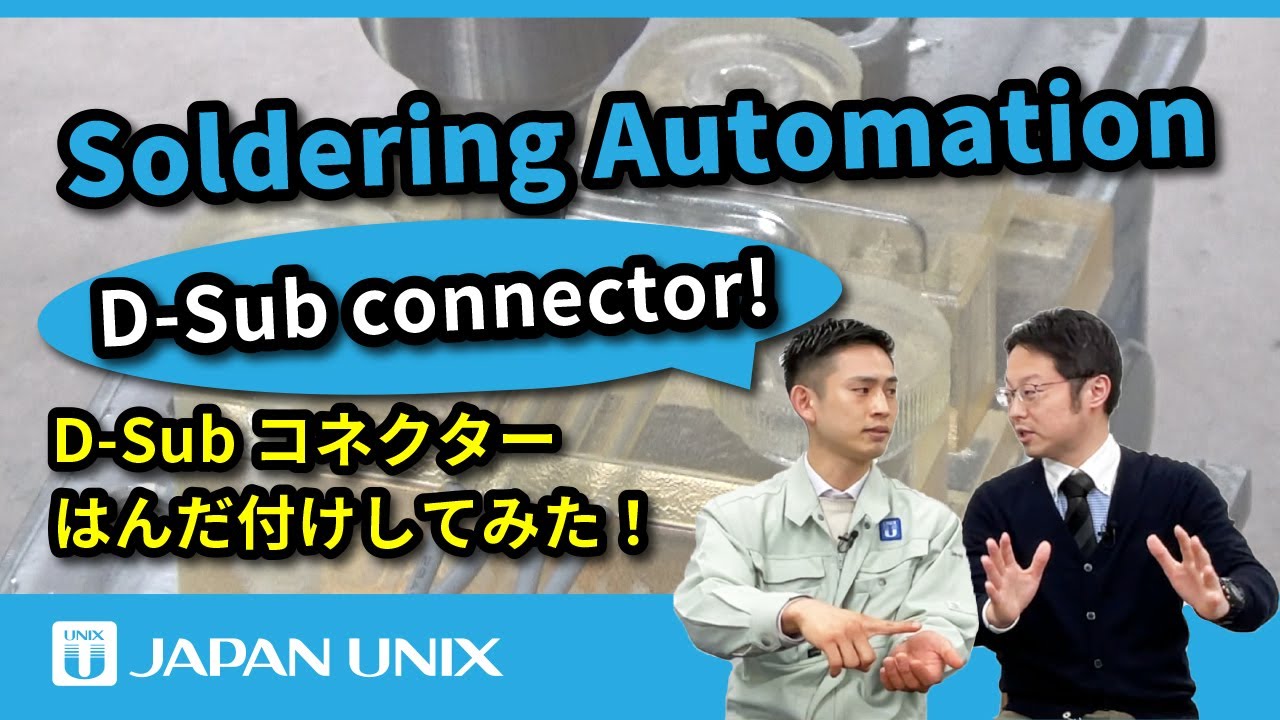