インタビュー:大手製造業にて40年のキャリアを持つ生産技術者とともに振り返る -後編-
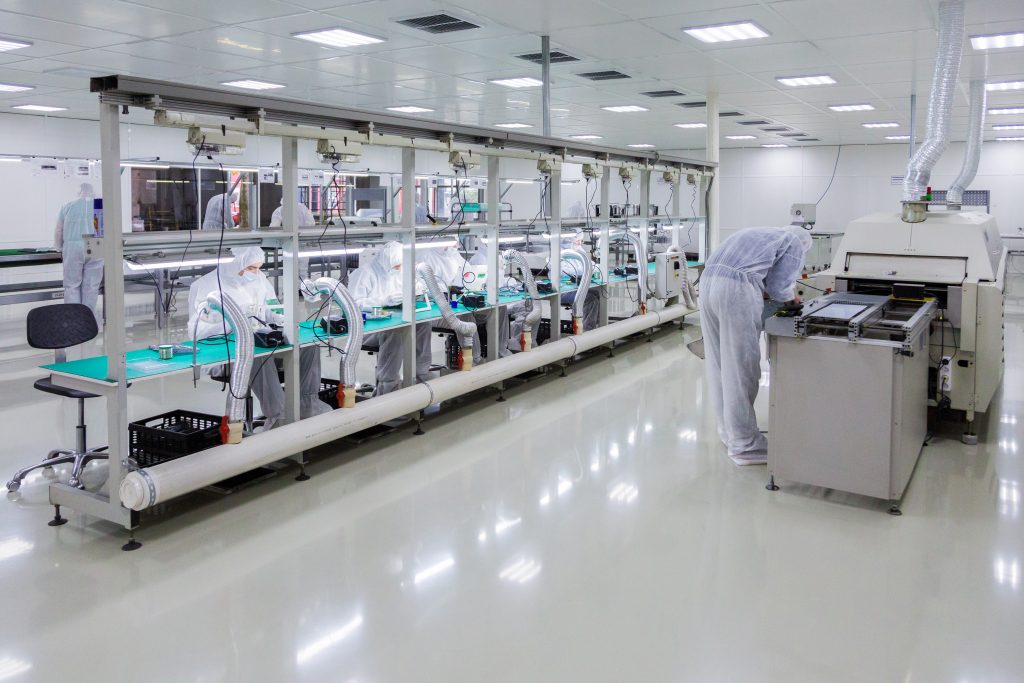
導入事例インタービュー
40年キャリアを持つ生産技術者 -後編-
目次
- 2000年代になるとどうなるのですか?
- 熟練作業者の技をレーザーはんだ付けで実現
- 社内でロボット導入をスムーズに進めるコツ
- ロボット導入はスタート地点。動かし続ける重要性
- 次世代の生産技術者へアドバイス
- 今回の参考動画
ロボットによる難作業の自動化へ開発をシフトした2000年代
竹串は細いながらも硬質で安価、部品を傷つけにくく、帯電しにくいなど電子製造では今も人気のツール
2000年代になるとどうなるのですか?
2000年代以降になると、主要な生産拠点が海外に移り、主な業務はこれまでに開発して現場に導入した装置の保守や改修が多くなっていきした。そしのため、高度生産技術として「熟練した匠の技」をロボットで自動化するの取り組みが始まりました。
これまでの装置は、利益率の高い製品を大量生産するために、高速で高品質のはんだ付けを自動化することに注力してきました。しかし、海外拠点へ生産を移転したため、国内のラインに残ったのは、熟練した技能者でなければ難しい作業ばかり。そこが生産のボトルネックになっていることも多く、それを自動化して技術承継をすることに力を入れました。
例えば、センサなどから伸びるケーブルやハーネスは、細い電線が何本も集まって1本になった多芯の電線になっています。その製造工程では、外皮と中の電線1本ずつ皮を剥いて、電線を基板やコネクタの所定の位置に置いてはんだ付けをします。芯線は細くて柔らかく、皮を剥く時に微妙に曲がっていたりするため、決まった位置に決まったものが置かれるプリント基板への電子部品のはんだ付けに比べて難易度が上がります。しかし、それでも品質を担保しなければならず、ロボットではなかなか難しい作業のため自動化が進まず、人手に頼っていました。
熟練作業者は、はんだごてを駆使するだけでなく、竹串やピンセットなど様々な道具を使いこなして作業をしている状態で、まさに匠の技でした。
熟練作業者の技をレーザーはんだ付けで実現
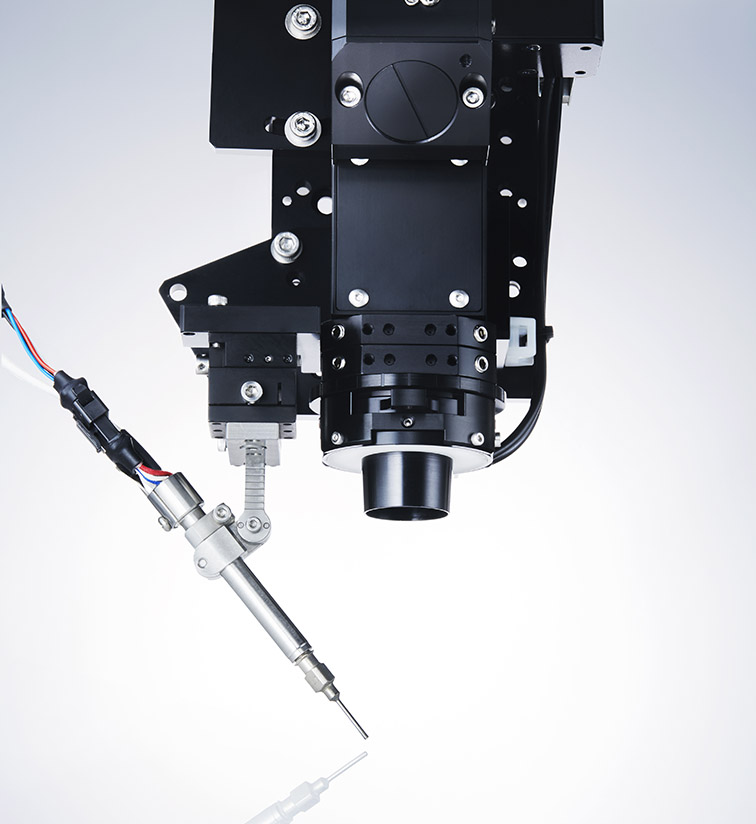
そうした難しい作業の自動化を進めていったということですね
もし、担当作業者が離職したら生産できなくなりますし、受注が増えた際に生産数を上げることができません。そのため、各作業を標準化して、自動化することに取り組みました。
ジャパンユニックスさんにも協力して頂き、プロトタイプを開発しました。レーザーはんだ付けを初めて採用し、カメラで部品を認識して、前後工程の情報をもとに条件を抽出し、はんだ付けの自動化が実現しました。ジャパンユニックスのレーザーはんだ付けを選んだ理由は、長年はんだ付け装置を使ってきて実績と信頼があったこと、温度管理と制御機能がとても優れていたことです。測定した温度がグラフで表示され、精度も高い。はんだ付けにとって温度制御がとても重要だと認識しているところ、はんだ付けの知識をきちんと持っていることが大変素晴らしかったです。
社内でロボット導入をスムーズに進めるコツ
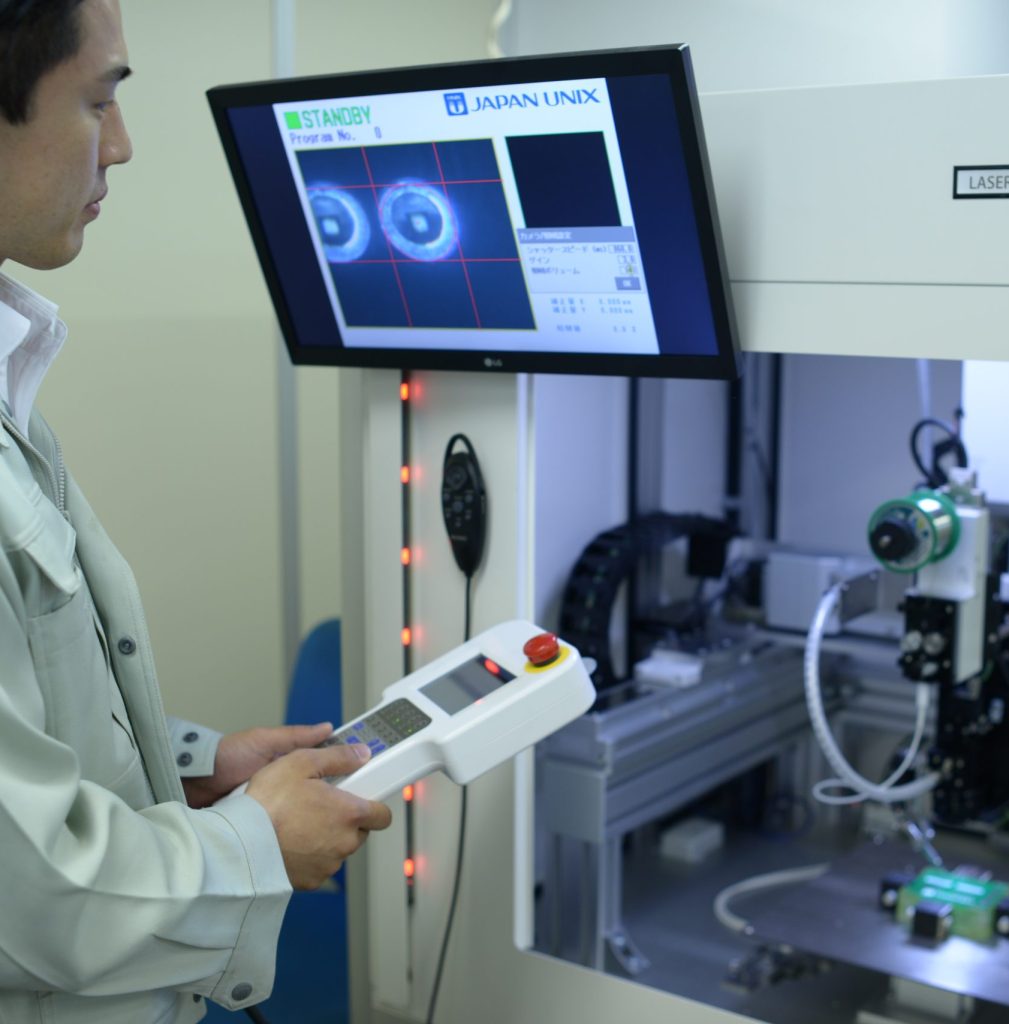
ロボットの導入をスムーズに進めるにはどうしたら良いでしょうか?
製造現場ではんだ付けロボットを導入したくとも、上司や経営者の立場からすると、導入の費用対効果や設備投資の回収計画はどうなるのかが気になる点だと思います。単純に投資金額を生産数量で割り算してROIを示しただけの提案では弱く、そこには現場が抱える問題点とその解決策も入っていません。投資対効果を紐解いて細かく因数分解して、さまざまな角度から導入メリットを示していくことが大事です。例えば、専用機は特定製品の生産が終了したら終わりですが、ロボットはプログラムを変更して別製品の生産ラインでも利用可能です。昨今であれば人手不足で人が採用できないこと、トレーニングも難しいところをロボットならそれを解決できるといったメリットを積み上げて提案していくのが良いと思います。
ロボット導入はスタート地点。動かし続ける重要性
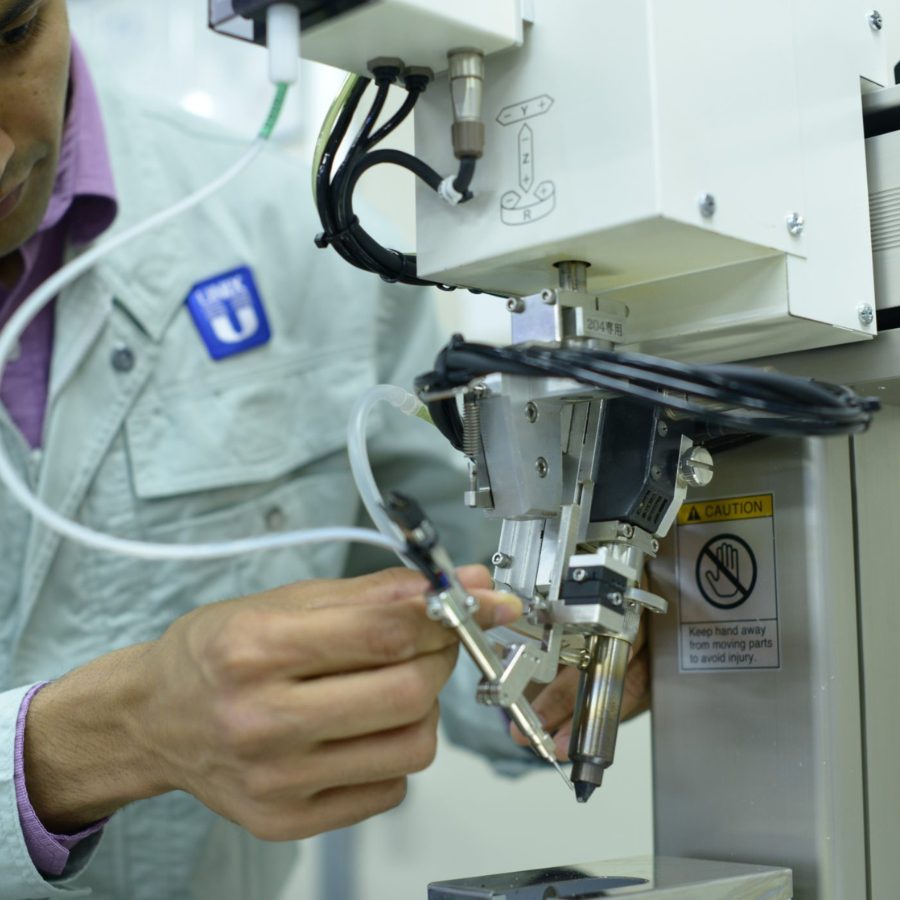
導入後に気をつける点はありますか?
はんだ付けロボットは、導入して終わりではなく、いかに長く動かし続けて利益を産むかが大切です。そのためには日々のメンテナンスや定期的な部品交換やオーバーホールを欠かさずにやることが最低条件ですが、この単純なことが非常に難しいのです。現場でメンテナンスするように言ってもなかなか守られず、そうした積み重ねが機械にダメージを蓄積させていくことになります。
私が実践して効果があったのは、実際のはんだ付けの状態とはんだごての小手先の消耗具合、不良発生のメカニズムを生産ラインの担当者にデータで示して、メンテナンスのマニュアルやルールの根拠を丁寧に説明しました。毎日の少しの手間で良品率が上がりかつ安定し、急に装置が止まることもなくなることを理解してもらいました。その結果、日常業務のひとつとなり、装置寿命も延びていきました。
次世代の生産技術者へアドバイス
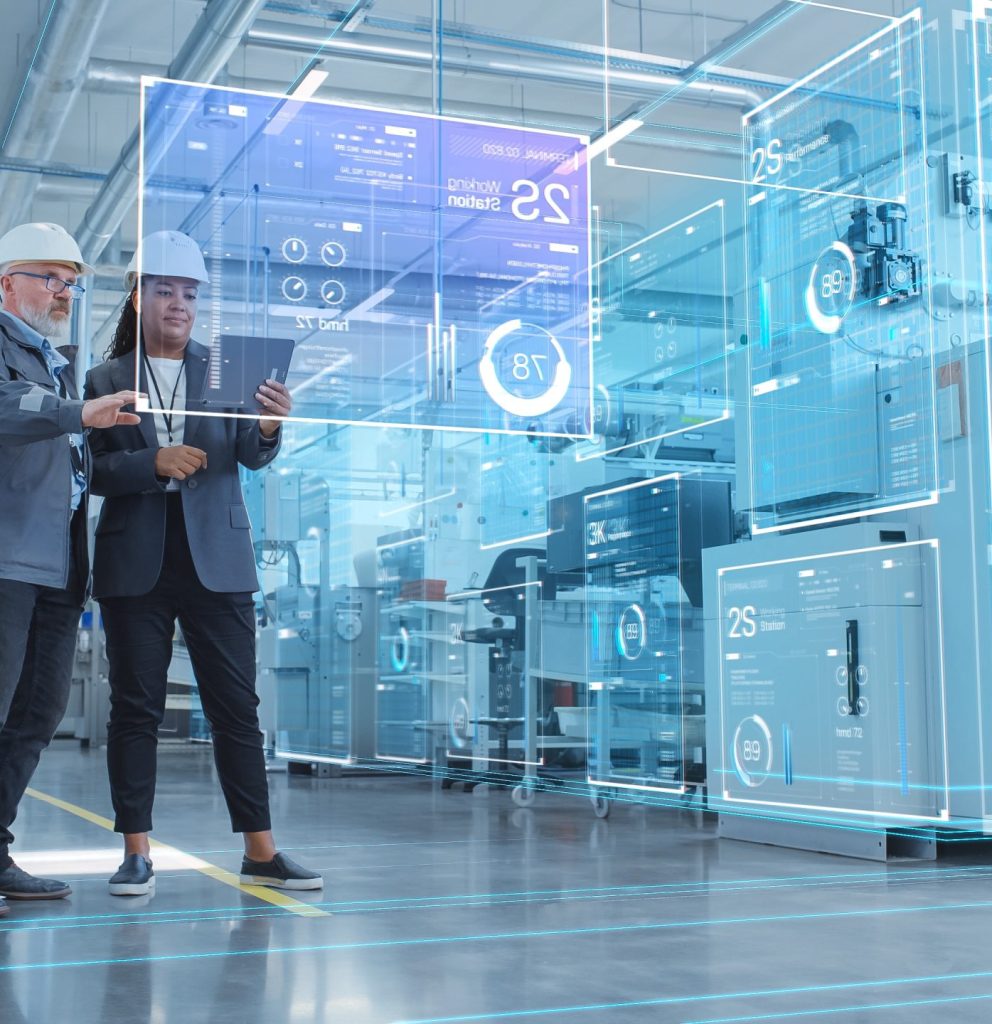
40年を振り返り、次世代へのアドバイスを
1980年代や1990年代は大量生産で稼いできた時代です。その後、中国をはじめ生産拠点が海外に移り、国内は多品種小ロットになっていき、採算ギリギリのロットしか作らなくなっています。そうなると新たな設備投資も厳しくなります。
そんな状況のなかでも、企業は存続しなければならないし、次の時代に向けて技術と技術者を残していかなければなりません。でも今は人の採用は難しいこともあり、ロボットによって製品の単価や価値を上げていくことが私たちに求められていることだと思います。必要なことは、単に量産のことだけを考えるのではなく、いかに利益率が高い製品を設計し、且つそれを製造する工程を作るか、が大事だと思います。
量産が必要となれば海外工場に展開する。国内ではマザー工場、研究開発の機能をしっかりと確立することが大切で、生産技術の分野ではロボットを活用した取り組みは欠かせないものだと思います。
関連製品・サービス
参考動画
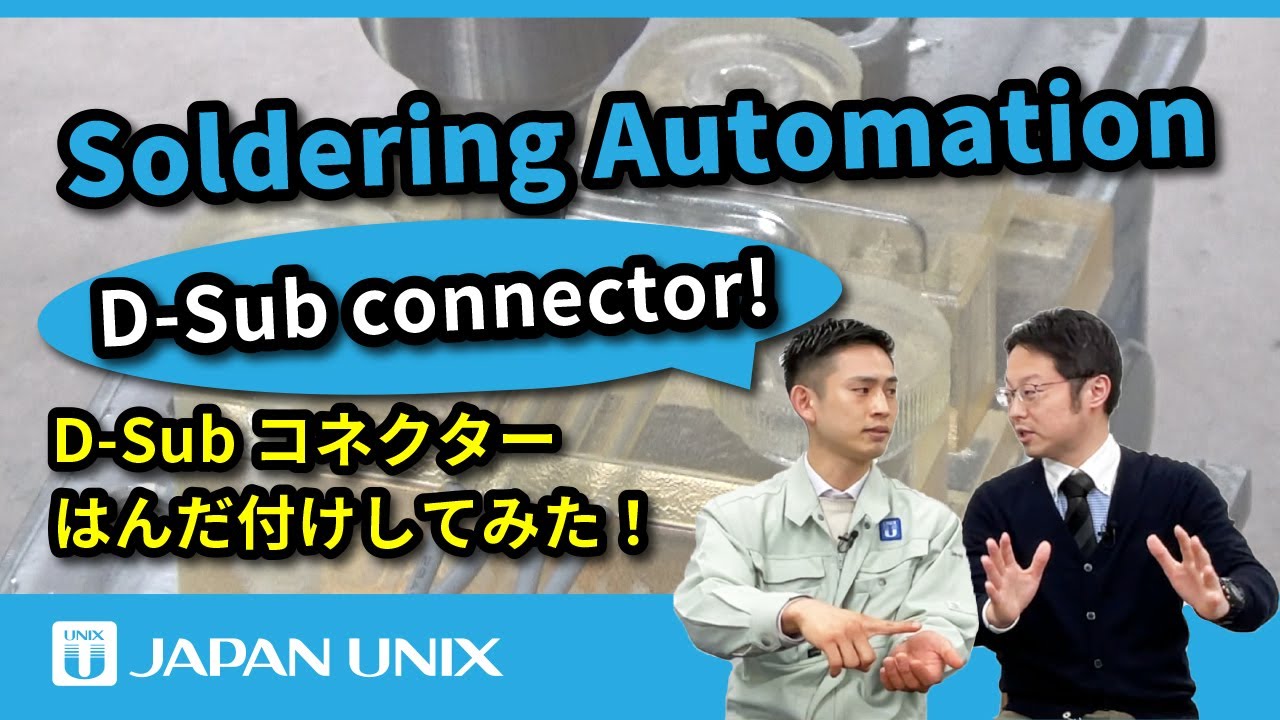