セレスティカ・ジャパン
NEC宮城から外資系EMSへ。
組織転換の核となったIPC標準
国内特定顧客向けの製造が主だった旧体制からグローバル市場で多種多様な製造受託へと移行
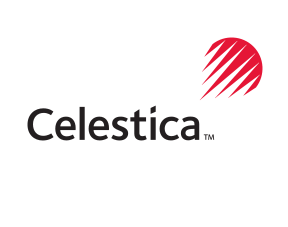
セレスティカは、カナダのトロントに本社を置く、世界トップ5のグローバルEMSである。2002年に旧宮城日本電気株式会社(NEC宮城)を買収する形で日本法人が発足。国内特定顧客向けの製造中心からグローバルEMSへと移行した背景には、IPCを活用した国際標準への対応があった。その導入経緯と効果について、日本で唯一(2016年3月時点)のIPC-A-610マスタートレーナーである、千葉達也様(現在、弊社に転籍済)に話を伺った。
社名 | セレスティカジャパン株式会社 (旧NEC宮城) |
---|---|
創立 | 2002年 (日本法人)、1994年(グローバル) |
売上高(連結) | 5,600万USD (約6,000億円) |
従業員数(連結) | 約25,000人 |
事業内容 | 電子機器の受託製造サービス。事業者向け製品の製造を請け負い、特に通信機器を得意とする。製造だけでなく、設計から修理までメーカーに代わって請け負うことができ、近年は、航空宇宙産業や防衛機器、産業機器、エネルギー機器、ヘルスケア機器、半導体製造装置など、多品種少量生産で高品質が求められる付加価値品の生産も増加 |
詳しくお知りになりたい方は、こちらからPDFファイルをダウンロードいただけます。
IBMからのMBO。NEC宮城・山梨の買収による日本法人設立
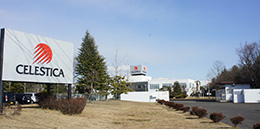
御社の概要を教えてください。
当社はカナダに本拠を構える、1994年創業のEMSです。もとはIBMのカナダ工場だったものを当時の経営陣がMBOして発足しました。ちょうど世界で、EMSのビジネスが生まれ出した頃のことです。
セレスティカジャパンは、NECの通信システムの開発・製造拠点だったNEC宮城とNEC山梨を、セレスティカが買収してスタートしました。現在は、国内の通信キャリアの光伝送装置や局内装置のほか、NECや国内外の大手メーカーの通信機器を製造しています。また、防災無線用の操作盤や半導体製造装置、人工衛星向けの超精密プリント基板など、本社と同様、多様化製品市場に注力しています。
NEC時代からグローバル市場を見据えた国際標準化体制へ。
世界のEMSでは、2002年から当然のようにIPCを導入。
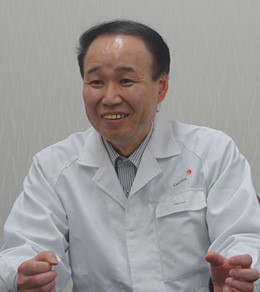
IPC-A-610 MIT 千葉達也様
IPCに取り組みはじめた経緯を教えてください。
NEC宮城時代の2000年頃に、当時の経営陣から、海外の規格を勉強しておくように指示をされたのが始まりです。当時、海外では企業間のM&Aが盛んで、業界再編が活発でした。
国内はまだエレクトロニクス業界が健在でしたが、少しずつ変化しはじめていた時期です。経営陣は先行きが不透明な時代に対応するため、海外EMSを活用した効率化や、自らが国内外のあらゆる企業から製造受託を受けEMS事業を強化することなど、経営改革を進めていました。
NEC時代にIPCを取り入れていたとは意外でした。てっきりセレスティカになってからIPCを取り入れたものと思っていました。
そうですね。当時の経営陣は先見の明があったのだと思います。NEC時代は国内大手通信キャリア向けの製品を作る専門工場のような形でした。しかし、『これから先は、それだけでは経営リスクが大きく、他の企業からも仕事を取っていかなければいけない』と言われた記憶があります。上司に指示を受けてからは、世界にはどんな規格があるのか調べるところから始めました。そしてセレスティカやソレクトロン(現Flextronics)、フォックスコンなど海外大手EMSについて調べるうちに、彼らが当然のようにIPCを導入していることを知りました。
国内独自規格と国際標準の併用。自社基準とIPCを比較し、徐々に国際標準へ適合。
当時の自社基準とはどういうものだったのですか?
当時、最も大きな顧客は、国内最大手の通信キャリアで、まずその顧客独自の伝送規格がありました。それを自社用に噛み砕いたものが自社基準です。取引先の伝送規格と自社基準を併用して使っていました。IPCを導入した後は、自社基準とIPCを比較し、合致した部分としなかった部分を洗い出し、それぞれに判定基準を明確にして自社基準をIPCスタンダードに合わせるようにしていきました。いまも取引先通信キャリアの伝送規格と自社基準、IPCを併用して使っています。
自社基準・国内標準では、世界で理解されない。
宮城という地でグローバルな商売が出来るのは、IPCがあればこそ
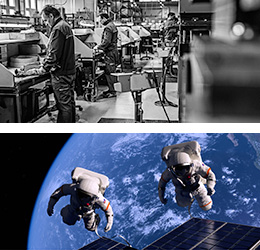
IPCを採用したメリットは?
2002年の買収に際し、セレスティカによる工場査察がありました。当社以外にもいくつかの工場の買収を検討していたようですが、最終的には当社とNEC山梨に決まりました。当時すでにIPCを導入していたので、セレスティカの求めることが理解できたことが大きかったのではないかと思います。もし、IPCすら知らない状態だったら、今はなかったかもしれません。
またEMSは、さまざまなお客さまから仕事を受託します。通信機器だけではありません。IPCをはじめる前の自社基準はあくまで伝送規格であり、通信機器以外のお客さまにはまったく響きませんし、理解もされません。IPCは電子部品の実装に関する規格であり、EMSのための規格のようなものです。どんな分野のお客さまにも対応できるようになったというのは大きなメリットです。
もうひとつ大きなことがあります。
宮城というローカルな地に拠点を構える企業が、世界を相手に商売を続けていられるのは、IPCがあればこそです。NECという大きな看板がなくなり、さまざまな変化がありました。例えば、人材採用でもNEC宮城だった頃に比べて応募してくる人数は大きく変わりました。でも最近は、東京に行かなくても宮城でグローバルな仕事をしたいという積極的な人材が増えてきました。地方にいながらにして世界とビジネスができる基盤があるのはとても大きいと感じています。
EMSの共通課題とは、『お客さまによって要求が違うこと』
IPCを採用し、標準的な工法で製造コストの削減
実際にIPCをどのように活用しているのですか?
原本をそのまま使っています。判断に迷った時などにIPCの原本を見て判断するようにしています。
EMSの難しいところは、お客さまによって要求が違うということです。だから、お客様基準を解釈して、製造する製品毎に自社基準を全て作っていたら時間も手間もコストもかかってしまいます。その点、IPCは汎用性が高く、ほとんどのお客さまの要求に対応できます。万能で助かっています。
IPCは、イラストと写真による図解と解説が詳しく掲載されていて、誰でも見やすくなっています。社内基準とIPCを合わせて使うことにより、正確でスピーディーに良/不良の判別がつけられるようになります。
日本企業は、各社が独自基準を作り、部材も標準部品を避ける傾向があります。独自基準と特注部品が高付加価値を生み、差別化になると思っている節があります。しかし、標準部品を使い、IPCのような国際標準規格を採用して標準的な工法を使う事に慣れれば、今よりもっとコストを下げることができます。付加価値や競争力は、その製品におけるコアな部分や機能に絞ることが重要です。
詳しくお知りになりたい方は、こちらからPDFファイルをダウンロードいただけます。